1. ¿Qué es un semiconductor?
Los semiconductores son materiales con propiedades electrónicas únicas, cuya conductividad eléctrica se sitúa entre la de los conductores y los aislantes. Los materiales semiconductores se utilizan para fabricar componentes como transistores y diodos, que son fundamentales en los equipos electrónicos.
Los semiconductores se emplean en dispositivos simples como celdas solares y LEDs, pero más comúnmente se procesan en chips que impulsan circuitos integrados (CI), microprocesadores, memorias y módulos de comunicación como Bluetooth, Wi-Fi y telecomunicaciones móviles. También juegan un papel clave en sistemas como los frenos ABS.
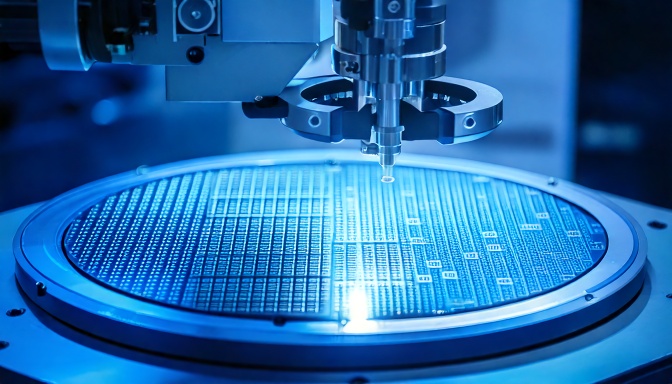
[1]
2. ¿Qué es un CI (circuito integrado)?
Un circuito integrado (CI), también conocido como microchip o simplemente chip, es un componente electrónico que integra millones de transistores y otros elementos (como resistencias y capacitores) en un pequeño sustrato semiconductor, generalmente de silicio. Este sustrato se conoce como chip, por lo que los CI suelen denominarse chips. Estos elementos integrados colaboran para realizar diversas funciones, como el procesamiento de datos, almacenamiento, amplificación de señales o actuar como osciladores, contadores o compuertas lógicas.
[2][3]
3. ¿Qué es una oblea? La diferencia entre una oblea y un chip
En electrónica, una oblea es una fina lámina circular de material semiconductor, generalmente de silicio, que sirve como base para la producción de microchips. Durante el proceso de fabricación, se depositan múltiples capas de materiales sobre la oblea y se graban patrones intrincados para formar circuitos integrados. Luego, la oblea se corta en numerosos componentes individuales conocidos como chips.
[4][5]
4. Cadena de Suministro de Semiconductores
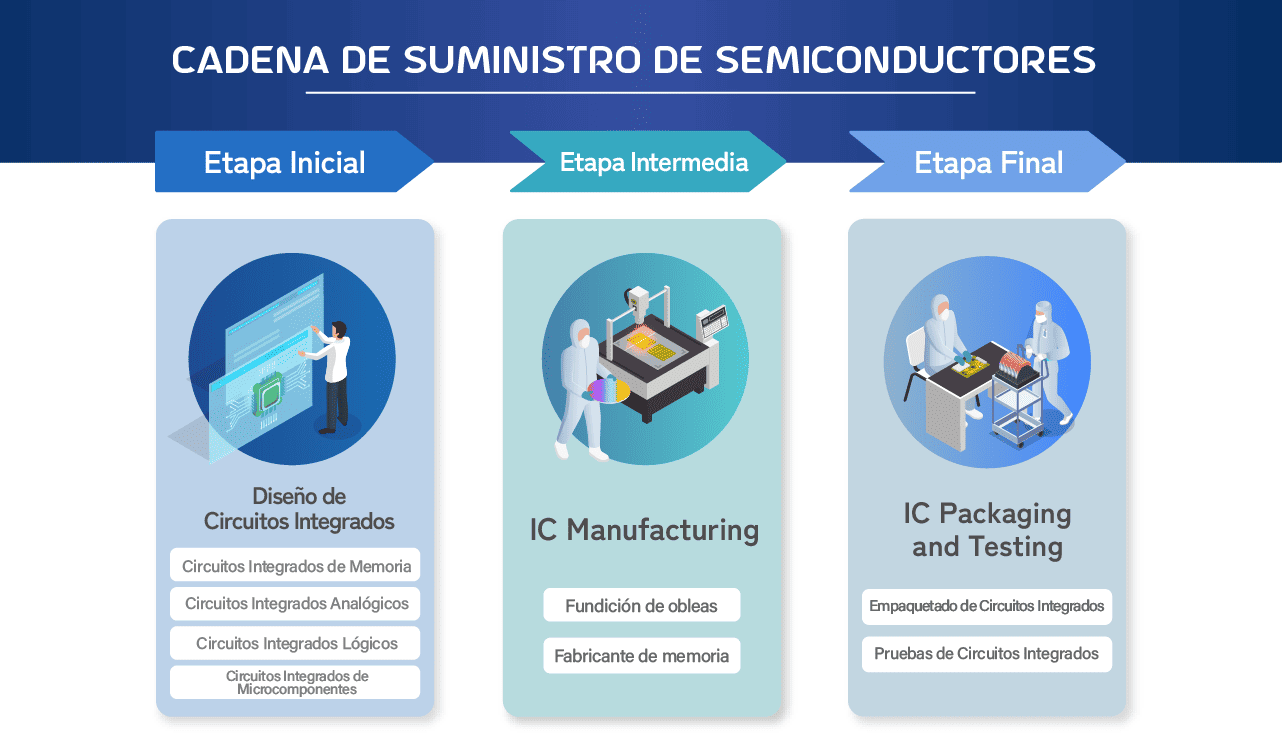
La cadena de la industria de semiconductores se puede dividir en tres segmentos: diseño de circuitos integrados (IC), fabricación de IC y empaquetado y pruebas de IC.
Muchas empresas de diseño de IC son "fabless", lo que significa que diseñan y venden chips pero subcontratan los procesos de fabricación y prueba. Algunas empresas destacadas de este modelo incluyen Qualcomm, NVIDIA, Broadcom y empresas taiwanesas como MediaTek, Novatek y Realtek.
La fabricación de IC está a cargo de fundiciones como TSMC y UMC en Taiwán, y GlobalFoundries. El empaquetado y prueba de IC se realizan a través de empresas OSAT (Outsourced Semiconductor Assembly and Test) como ASE y SPIL de Taiwán, además de Amkor y JCET.
También existen los fabricantes de dispositivos integrados (IDM, por sus siglas en inglés) como Intel, Samsung Electronics y Texas Instruments. Estas empresas diseñan, fabrican, empaquetan y prueban sus propios chips, gestionando todos los segmentos de la cadena de la industria de semiconductores con capacidades de producción completas.
1 ) Industria de Semiconductores Upstream
El segmento upstream de la industria de semiconductores se centra en el diseño de circuitos integrados, donde las empresas crean y verifican funciones de chips, convirtiendo conceptos en diseños de circuitos integrados.
- ICs de Memoria: Almacenan datos e instrucciones de programas; se encuentran en PC, teléfonos inteligentes, consolas de videojuegos y cámaras digitales.
- ICs de Microcomponentes: Incluyen CPUs y GPUs, encargadas del procesamiento de datos y comandos; se usan en teléfonos inteligentes, electrónica automotriz y electrodomésticos.
- ICs Lógicos: Realizan operaciones lógicas y controlan señales; se usan en dispositivos de comunicación, electrónica automotriz y automatización industrial.
- ICs Analógicos: Procesan señales continuas como voltaje y corriente; se utilizan en equipos de audio, comunicación inalámbrica, gestión de energía y sensores.
2 )Industria de Semiconductores Midstream
Una vez finalizado el diseño del CI, comienza la fase de producción. El segmento midstream de la industria de semiconductores—fabricación de CI—implica la producción y el procesamiento de obleas, donde los circuitos diseñados se fabrican sobre las obleas para crear chips (CI).
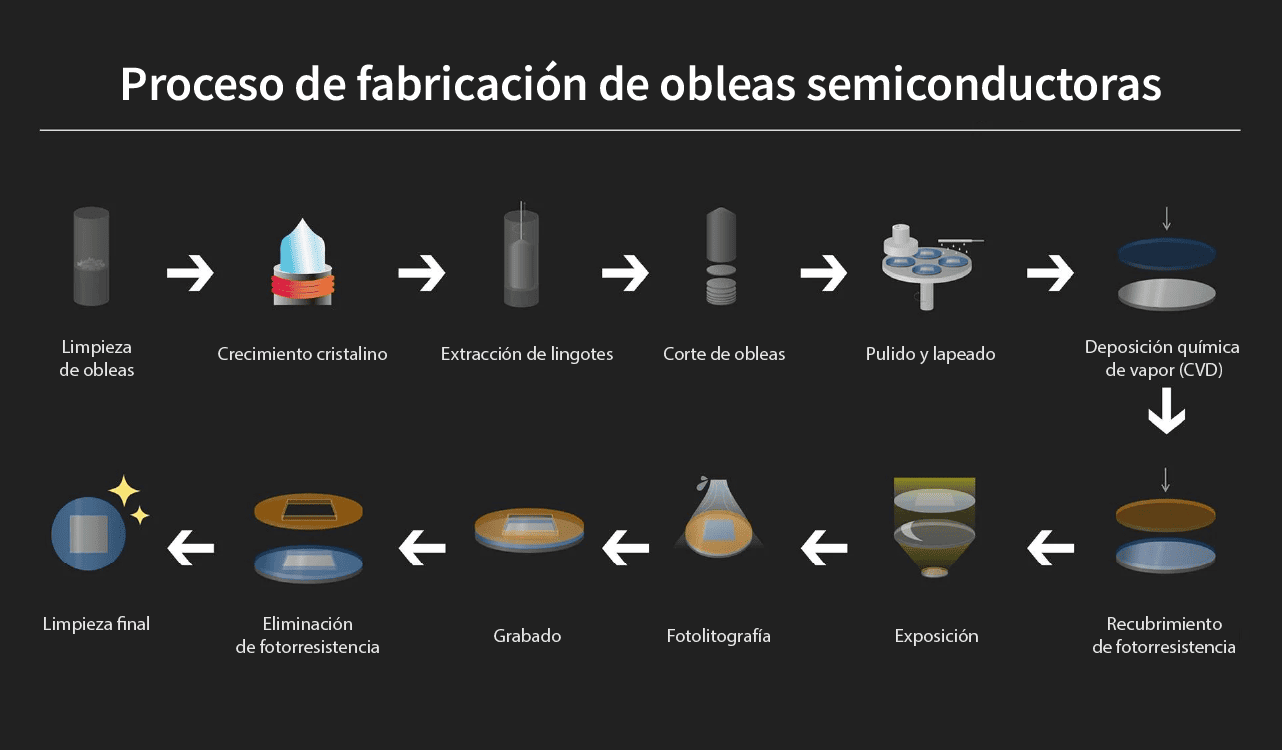
3 ) Industria de Semiconductores Downstream
Después de la fabricación, el siguiente paso es inspeccionar la funcionalidad de las obleas. El segmento downstream de la industria de semiconductores implica el empaquetado y prueba de CI. Durante el empaquetado de semiconductores, la oblea producida en la fase de fabricación se corta en CI individuales, que luego se colocan en paquetes protectores que también proporcionan conexiones eléctricas. Posteriormente, las pruebas de CI aseguran que los chips empaquetados funcionen correctamente y cumplan con las especificaciones de rendimiento. Solo después de estos pasos, los CI se convierten en productos finales listos para el mercado.
5. ¿Cómo se fabrica una oblea?
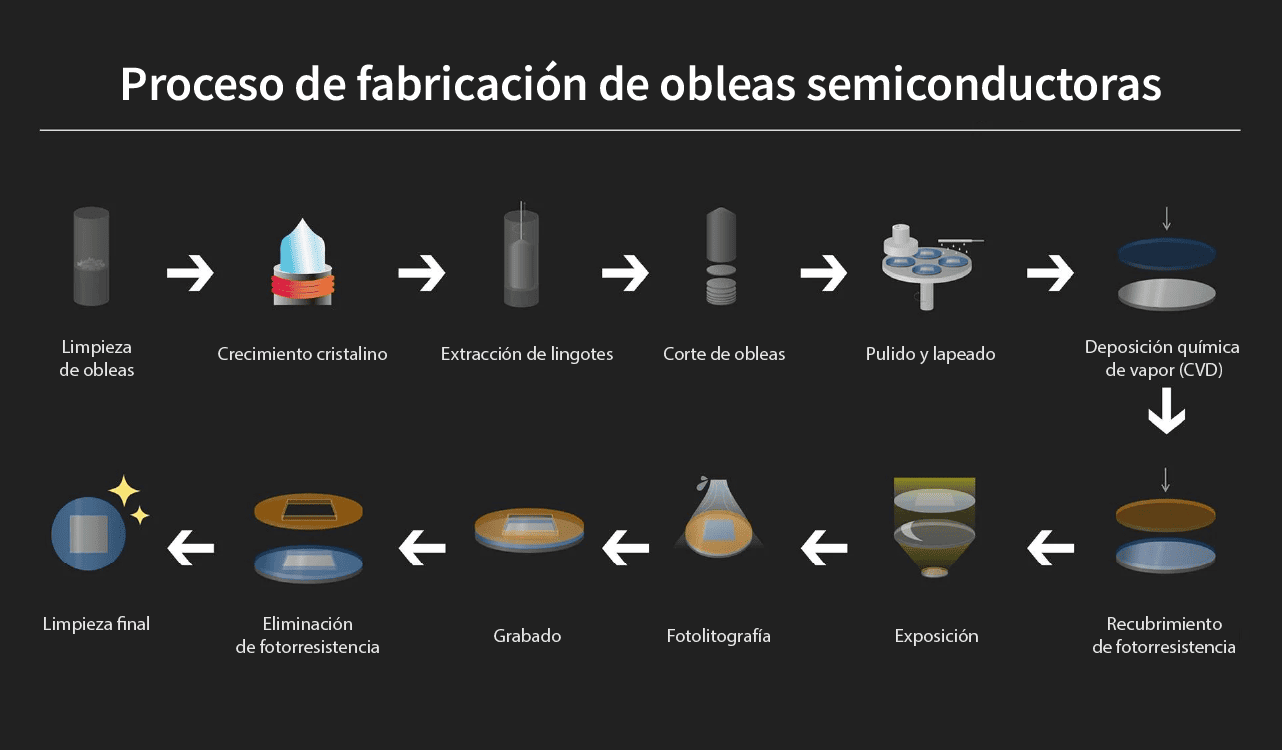
[6]
¿Cuál es la diferencia entre una oblea y un chip? Una oblea sirve como el material inicial para la fabricación de chips. Es un sustrato circular delgado de silicio, típicamente hecho de silicio monocristalino. El proceso de fabricación de obleas involucra dos etapas principales: la primera etapa, que incluye la limpieza de obleas, crecimiento de cristales, extracción de lingotes, corte de obleas y pulido; y la segunda etapa, conocida como fabricación de obleas, que incluye procesos como deposición de vapor, recubrimiento de fotorresistencia, exposición, revelado, grabado, eliminación de fotorresistencia y limpieza final.
Limpieza de obleas
Las superficies de los materiales en bruto de la oblea se limpian mediante fusión a alta temperatura y solventes como ácido fluorhídrico (HF) o hidróxido de potasio (KOH) para eliminar contaminantes y residuos orgánicos, garantizando una excelente calidad del sustrato.
Crecimiento de Cristales
El material de silicio de alta pureza, el dióxido de silicio, se coloca en un horno para su refinamiento, reduciéndolo a silicio de grado metalúrgico. Luego de la purificación por destilación, pasa por un proceso de descomposición lenta para producir "silicio policristalino".
Extracción de lingotes
El silicio policristalino se funde con ácido bórico y fósforo en un crisol de cuarzo y luego, a altas temperaturas, se sumerge y se extrae un lingote de silicio monocristalino (semilla de cristal) mientras gira. El silicio se adhiere a la semilla de cristal y se solidifica uniformemente en la varilla, formando un lingote de silicio monocristalino en forma de columna.
Corte de obleas
La columna cristalina recién producida tiene una superficie irregular. Se requieren herramientas de diamante de grado industrial para su procesamiento, eliminación de extremos cónicos, ajuste de diámetro y corte en rodajas de obleas utilizando sierras de alta dureza o sierras de hilo.
Pulido y alisado
Después del corte de la oblea, la superficie queda rugosa y requiere pulido y esmerilado. El pulido busca hacer la superficie cristalina más lisa y brillante, mientras que el esmerilado redondea los bordes de la oblea en una curva uniforme.
CVD (Deposición Química de Vapor)
CVD es un proceso en el que se introducen precursores gaseosos en una cámara de reacción. Cuando estos gases entran en contacto con un sustrato calentado, generan materiales depositados, formando una película delgada en la superficie del sustrato, utilizada para crear capas aislantes o conductoras.
Recubrimiento de fotorresistencia
Cuando se expone a la luz, la fotorresistencia sufre un cambio químico. Inicialmente, se recubre una capa uniforme de fotorresistencia sobre la superficie de la oblea, lo que permite que sea eliminada o retenida en pasos posteriores de exposición y revelado, formando el patrón deseado.
Exposición
Utilizando patrones en la fotomáscara, se expone la capa de fotorresistencia a la luz ultravioleta. La fotomáscara se alinea sobre la oblea recubierta con fotorresistencia, lo que provoca una reacción química en las áreas iluminadas de la capa de fotorresistencia, iniciando una reacción fotoquímica.
Fotolitografía
Al exponer las obleas a una solución reveladora (que puede contener álcalis como hidróxido de sodio o hidróxido de potasio, junto con aditivos), se eliminan selectivamente las áreas no expuestas de la capa de fotorresistencia, dejando un patrón en las áreas expuestas.
Grabado
Mediante soluciones de grabado ácidas o alcalinas, se eliminan los materiales subyacentes en función del patrón en la capa de fotorresistencia, dejando intactas las áreas protegidas en la superficie de la oblea (áreas de fotorresistencia expuestas), formando las microestructuras del chip.
Eliminación de fotorresistencia
Después del revelado, la fotorresistencia residual se elimina mediante métodos químicos, térmicos o mecánicos, como soluciones de eliminación, para evitar efectos adversos en el rendimiento del dispositivo.
Limpieza final
Finalmente, los chips pasan por un proceso de limpieza secundaria, que puede involucrar solventes orgánicos o inorgánicos, surfactantes o técnicas de limpieza ultrasónica, para eliminar los residuos químicos y partículas del proceso de fabricación, garantizando que los chips producidos sean limpios y cumplan con las especificaciones.
Aplicación de caudalímetros y boquillas en la industria de semiconductores
Aplicación 1: Monitoreo del flujo de productos químicos
En la fabricación de semiconductores, el control preciso del flujo de líquidos químicos es crucial debido a los procesos complejos y delicados involucrados. Cada etapa del proceso de producción depende de un suministro químico preciso y tasas de flujo adecuadas, lo que impacta la calidad y estabilidad del producto final. Los caudalímetros desempeñan un papel fundamental en la supervisión y control preciso del flujo dentro de las tuberías, asegurando la calidad y el rendimiento del producto.
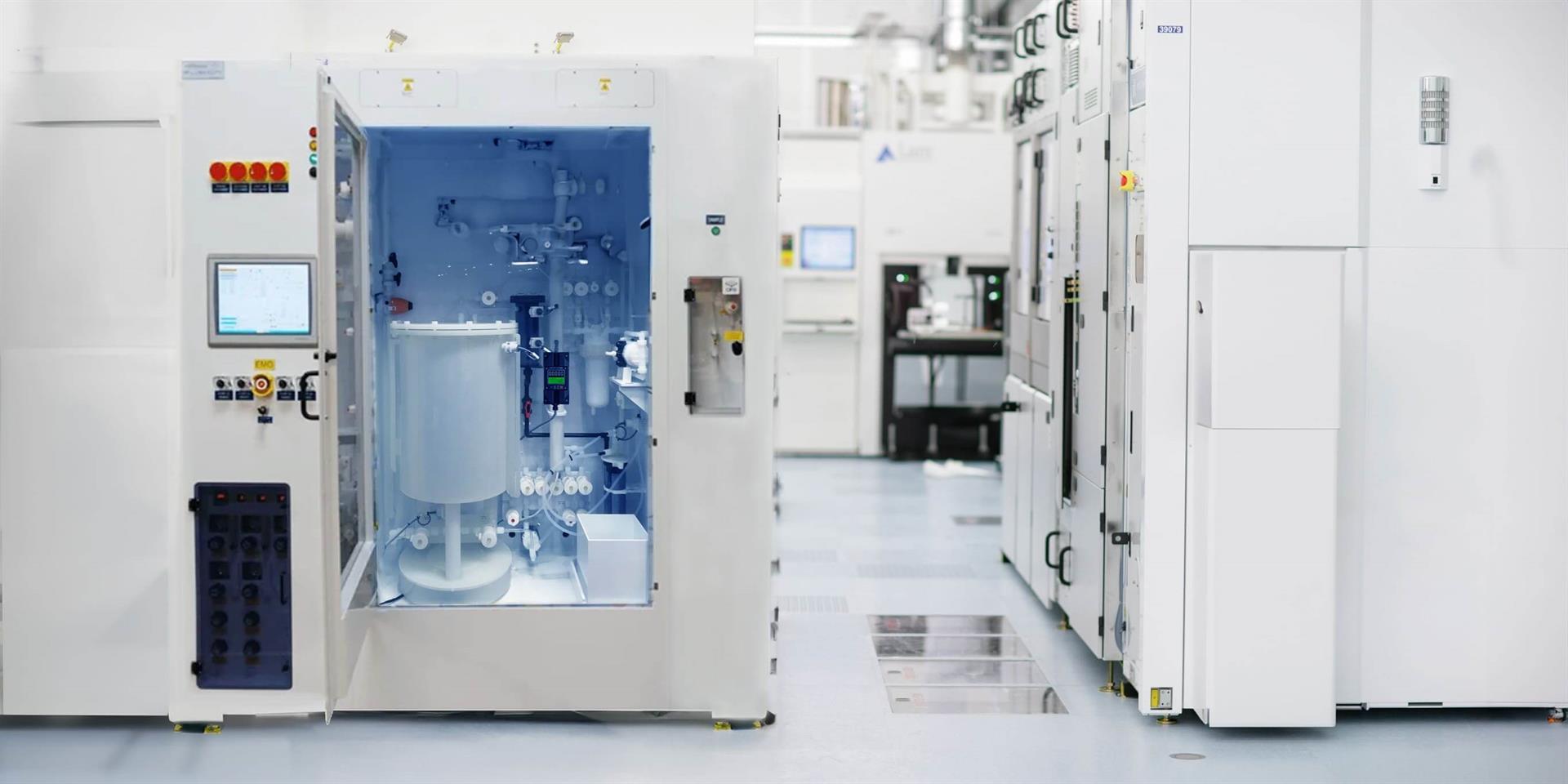
Ejemplo: Fábrica de semiconductores en China
Situación: Las fábricas tradicionales sin un sistema central de suministro de productos químicos suelen transportar diversos productos químicos de forma independiente a diferentes áreas y equipos. Esta práctica puede generar riesgos de seguridad y reducir la eficiencia en la optimización del uso de productos químicos.
Solución: Caudalímetro de rueda de paletas LORRIC FP-AS510
Para abordar este desafío, recomendamos la implementación de una sala de almacenamiento central de productos químicos dentro de la fábrica. Durante las operaciones, los productos químicos se suministran centralmente a cada máquina, y el caudalímetro de rueda de paletas FP-AS510 se utiliza para calcular con precisión las cantidades requeridas, reduciendo los costos de pérdidas químicas en los procesos. El FP-AS510, que cuenta con múltiples patentes y certificaciones internacionales, incorpora la tecnología patentada AxleSense. Su estructura de rueda de agua permite detectar flujos extremadamente pequeños a medida que los fluidos atraviesan el sistema, logrando una medición precisa del líquido. Además, el FP-AS510 ofrece capacidades de monitoreo en tiempo real para detectar condiciones anómalas de la pala, identificando problemas de flujo cero causados por la desaparición de la pala. Al instalar el FP-AS510, la empresa puede calcular con precisión las dosis para cada máquina durante la preparación de productos químicos, lo que se traduce en ahorros de costos. Además, dado que los productos químicos altamente concentrados y corrosivos pueden representar riesgos durante el almacenamiento y el transporte, el uso del FP-AS510 resuelve esta preocupación. El producto está fabricado con material PVDF, proporcionando una excelente resistencia a solventes y corrosión por ácidos y bases, eliminando preocupaciones sobre la corrosión y fugas de productos químicos, mejorando la seguridad en el lugar de trabajo.
Aplicación 2: Medición y Monitoreo del Agua Ultrapura
En la fabricación de semiconductores, se utiliza una gran cantidad de agua ultrapura para la limpieza de obleas, el enjuague de componentes electrónicos, el grabado y más. Durante el proceso de tratamiento del agua ultrapura, se requiere una medición precisa del flujo de líquido. Por ejemplo, en el proceso de ósmosis inversa (RO), medir el caudal del concentrado es crucial para controlar las proporciones de concentración y prevenir la incrustación de membranas. El monitoreo continuo del flujo de agua también ayuda a evaluar el rendimiento del equipo RO, detectando posibles fallos o anomalías a tiempo. En el proceso de desionización (DI), se utiliza resina de intercambio iónico para eliminar iones del agua, lo que requiere el monitoreo de los caudales a través de la resina y de los líquidos de retrolavado para garantizar una eliminación efectiva de iones. Además, el control preciso de la dosificación química es necesario durante la fase de adición de productos químicos en el tratamiento del agua ultrapura, como la medición de la dosificación de desinfectantes (cloro, dióxido de cloro, ozono) para la eliminación de microorganismos o de agentes de ajuste de pH (ácido sulfúrico, hidróxido de sodio) para mantener la estabilidad de la calidad del agua. Por lo tanto, las operaciones de tratamiento de agua ultrapura exigen una medición altamente precisa del flujo de líquidos y herramientas de medición resistentes a productos químicos.
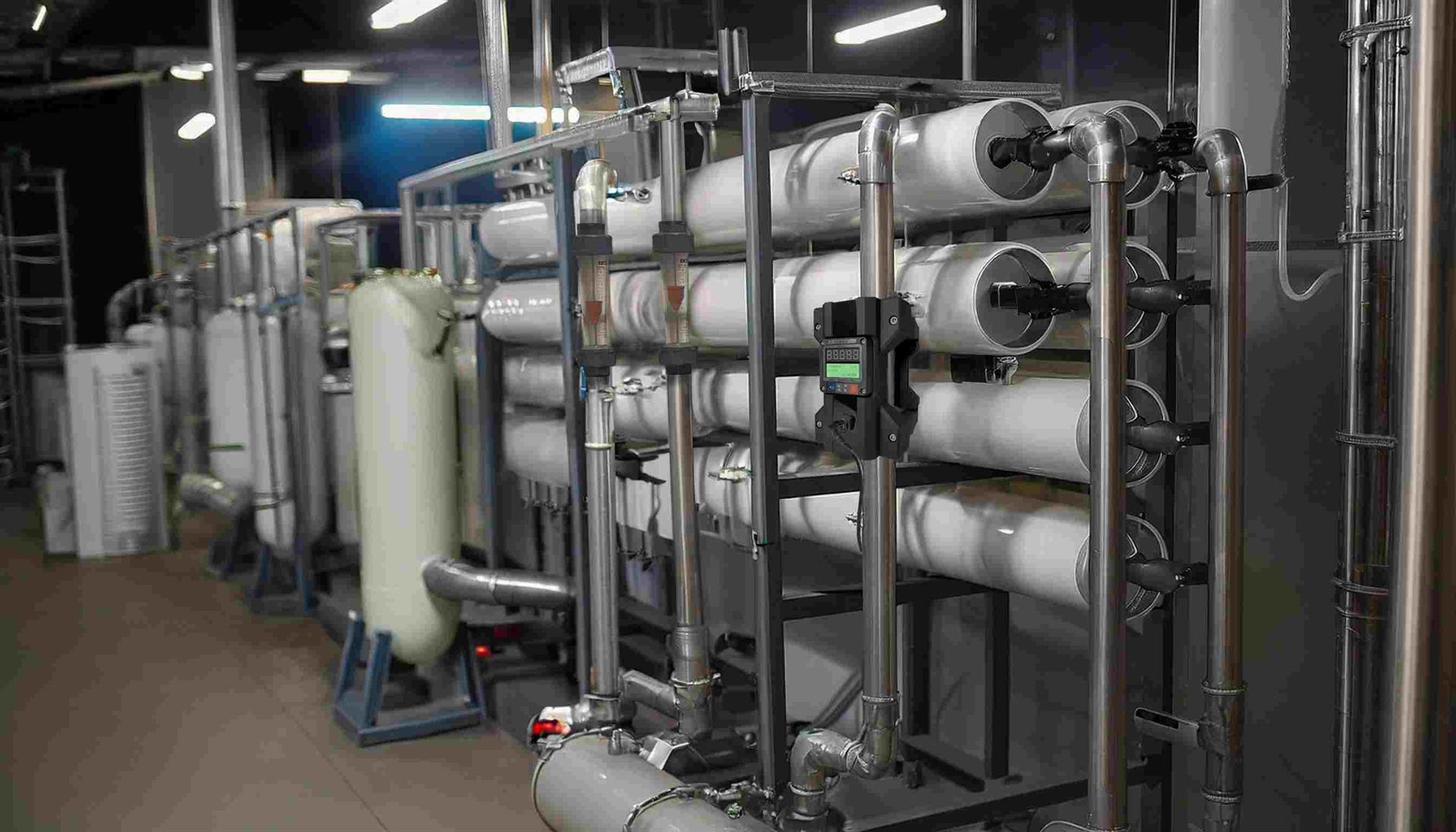
Ejemplo: Fundición líder de semiconductores en Taiwán
Situación: La empresa se especializa en sistemas de tratamiento de agua, incluyendo sistemas de agua ultrapura, reciclaje de aguas residuales y proyectos de tratamiento de aguas residuales. Durante la fase de tratamiento del agua ultrapura, los caudalímetros electromagnéticos estándar no pueden utilizarse porque el agua ultrapura no es conductora. La empresa buscaba una solución de caudalímetro ultrasónico, pero los modelos comunes en el mercado tenían procedimientos de instalación y configuración complicados. Además, requerían la reposición periódica de gel ultrasónico, lo que resultaba en una experiencia de usuario poco óptima. También necesitaban una solución para medir con precisión pequeños flujos de líquidos y garantizar una buena resistencia química durante el proceso de tratamiento de agua ultrapura.
Solución: Caudalímetros ultrasónicos de LORRIC
Recomendamos instalar los caudalímetros ultrasónicos de LORRIC en los equipos de tratamiento de agua ultrapura de la empresa. Estos caudalímetros cuentan con una instalación sencilla, medición de flujo bidireccional que elimina preocupaciones sobre la dirección del flujo, una pista de sonda patentada para una colocación precisa y sujetadores para un ajuste seguro. Esto mejora la precisión del flujo, garantiza estabilidad y permite la eliminación y el mantenimiento sin daños, simplificando el proceso de instalación. Los caudalímetros ultrasónicos de LORRIC utilizan dos sensores para medir la frecuencia de ondas ultrasónicas, calculando velocidades de flujo precisas. Son ideales para sistemas RO, monitoreando agua de alta concentración a través de membranas de ultrafiltración para garantizar la estabilidad, y para procesos DI, optimizando la eliminación de iones mediante resinas de intercambio iónico. Estos medidores ofrecen una excelente resistencia química, cumpliendo con los requisitos específicos del proceso.
Aplicación 3: Boquillas en espiral - Componentes clave en el tratamiento de gases de escape en semiconductores
En la fabricación de semiconductores, se generan gases nocivos (amoníaco, dióxido de azufre, dióxido de nitrógeno, ácido fluorhídrico, etc.) como parte de los gases de escape. Por ello, se utilizan boquillas en espiral en torres de tratamiento de gases de escape para rociar agentes de lavado como soluciones alcalinas (hidróxido de sodio) para neutralizar gases ácidos (amoníaco) o soluciones ácidas (ácido fluorhídrico) para neutralizar gases alcalinos (hidróxido de sodio, hidróxido de amonio). Este proceso convierte sustancias peligrosas en compuestos estables y manejables, purificando los gases de escape emitidos por la fábrica, asegurando el cumplimiento de las regulaciones de tratamiento de gases y promoviendo objetivos de desarrollo sostenible.
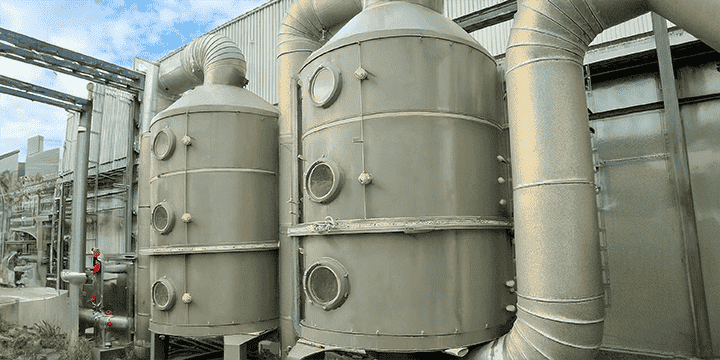
Ejemplo: Fundición líder de obleas en Taiwán
Situación: Las boquillas de marcas convencionales se producen principalmente mediante moldeo por inyección de plástico, creando modelos de boquillas directamente a partir de moldes. Este método de fabricación limita la capacidad de las boquillas en espiral para tener superficies en espiral de alta precisión y canales cónicos, lo que resulta en áreas de pulverización más pequeñas y un rendimiento menos efectivo. Además, las boquillas genéricas suelen utilizar PP (polipropileno), que carece de resistencia y dureza, es propenso a romperse y tiene una resistencia limitada a ambientes químicos de alta temperatura. Estas boquillas no solo no logran una cobertura de pulverización óptima, sino que tampoco tienen la resistencia a la corrosión requerida para el tratamiento de residuos en la industria de semiconductores.
Solución: Boquillas en espiral de LORRIC
Las boquillas en espiral de LORRIC se fabrican mediante mecanizado de precisión, esculpiendo materiales en boquillas sólidas de forma cónica en espiral. Sus caminos más amplios para objetos extraños evitan eficazmente la obstrucción por impurezas, y su cobertura de pulverización es mayor que la de otras marcas en el mercado, con ángulos de hasta 170 grados. Además, las boquillas en espiral de LORRIC están fabricadas con materiales altamente resistentes a la corrosión, como UPVC (cloruro de polivinilo) y PEEK (poliéter éter cetona), lo que prolonga su vida útil en entornos altamente reactivos químicamente. Son la mejor opción para el tratamiento de gases de escape en la industria de fabricación de semiconductores.