1. เซมิคอนดักเตอร์คืออะไร? (Semiconductor)
เซมิคอนดักเตอร์ คือวัสดุที่มีคุณสมบัติทางไฟฟ้าเฉพาะ โดยมีค่าการนำไฟฟ้าอยู่ระหว่างตัวนำและฉนวน วัสดุเซมิคอนดักเตอร์ถูกนำมาใช้ในการผลิตส่วนประกอบอิเล็กทรอนิกส์ เช่น ทรานซิสเตอร์และไดโอด ซึ่งเป็นส่วนสำคัญของอุปกรณ์อิเล็กทรอนิกส์
เซมิคอนดักเตอร์ ถูกใช้งานในอุปกรณ์ที่เรียบง่าย เช่น เซลล์แสงอาทิตย์และหลอดไฟ LED แต่โดยทั่วไปมักถูกนำมาผลิตเป็นชิปสำหรับวงจรรวม (IC) ไมโครโปรเซสเซอร์ ชิปหน่วยความจำ และโมดูลสื่อสาร เช่น Bluetooth, Wi-Fi และระบบสื่อสารมือถือ นอกจากนี้ยังมีบทบาทสำคัญในระบบต่าง ๆ เช่น ระบบเบรก ABS
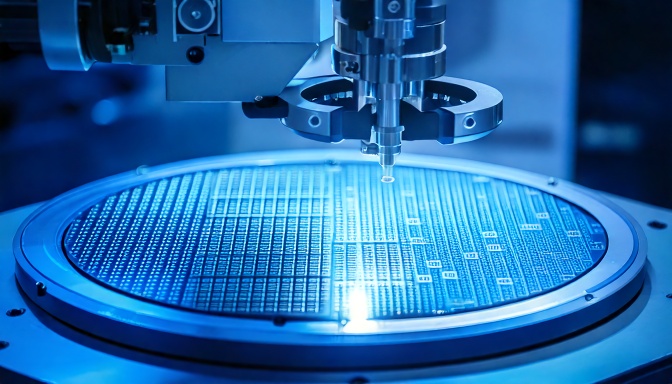
[1]
2. IC (วงจรรวม) คืออะไร?
วงจรรวม หรือที่เรียกว่าไมโครชิป หรือชิป คืออุปกรณ์อิเล็กทรอนิกส์ที่รวมเอาทรานซิสเตอร์และส่วนประกอบอื่น ๆ เช่น ตัวต้านทานและตัวเก็บประจุจำนวนหลายล้านตัวไว้บนแผ่นเซมิคอนดักเตอร์ขนาดเล็ก ซึ่งโดยทั่วไปจะทำจากซิลิกอน แผ่นเซมิคอนดักเตอร์นี้เรียกว่า "ชิป" ซึ่งเป็นเหตุผลที่วงจรรวมมักถูกเรียกว่าชิป องค์ประกอบที่รวมอยู่ในวงจรรวมจะทำงานร่วมกันเพื่อทำหน้าที่หลากหลาย เช่น การประมวลผลข้อมูล การเก็บข้อมูล การขยายสัญญาณ หรือทำหน้าที่เป็นออสซิลเลเตอร์ เคาน์เตอร์ หรือเกตลอจิก
[2][3]
3. เวเฟอร์คืออะไร? ความแตกต่างระหว่างเวเฟอร์และชิป
เวเฟอร์ในอุตสาหกรรมอิเล็กทรอนิกส์คือแผ่นบางรูปทรงกลมที่ทำจากวัสดุเซมิคอนดักเตอร์ เช่น ซิลิกอน ซึ่งใช้เป็นพื้นฐานในการผลิตไมโครชิป ในกระบวนการผลิต จะมีการเคลือบวัสดุหลายชั้นลงบนเวเฟอร์ และแกะสลักลวดลายที่ซับซ้อนเพื่อสร้างวงจรรวม (Integrated Circuit) หลังจากนั้น เวเฟอร์จะถูกตัดออกเป็นชิ้นเล็ก ๆ ซึ่งเรียกว่า "ชิป"
[4][5]
4. เวเฟอร์คืออะไร? ความแตกต่างระหว่างเวเฟอร์และชิป
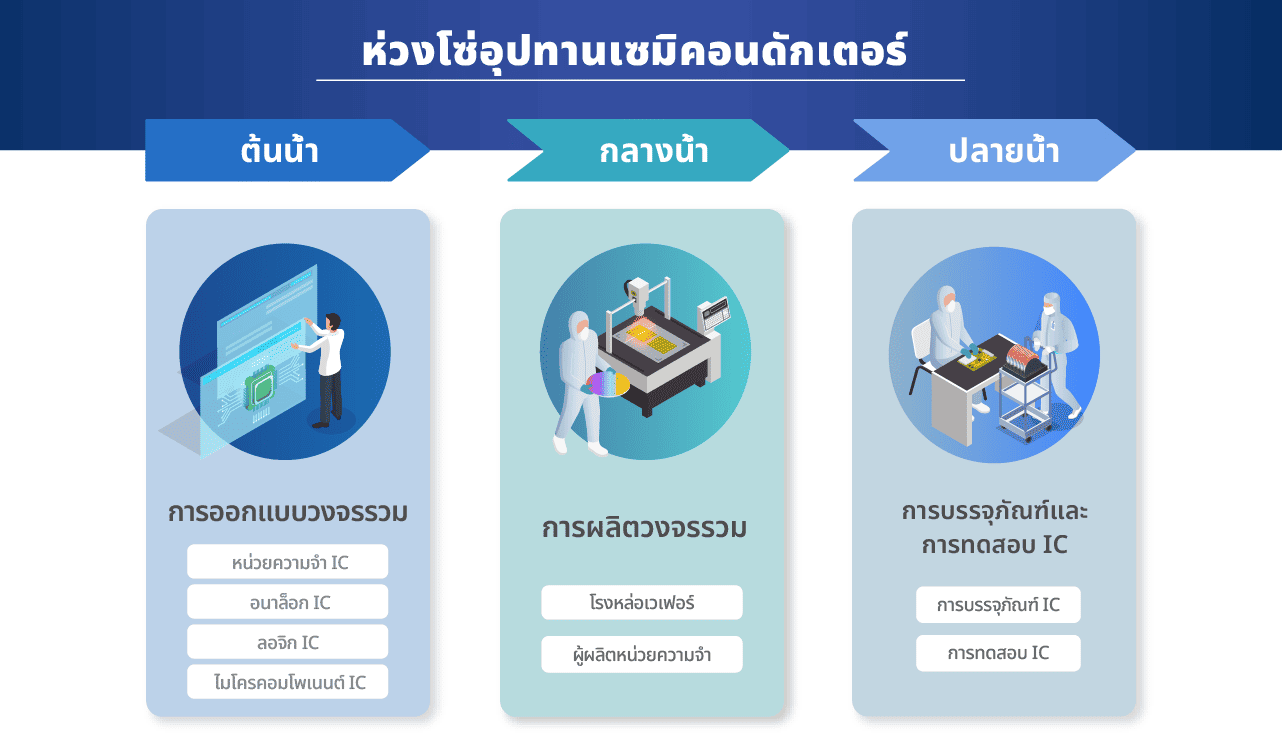
ห่วงโซ่อุตสาหกรรมเซมิคอนดักเตอร์สามารถแบ่งออกเป็น 3 ส่วนหลัก ได้แก่ การออกแบบวงจรรวม (IC design) การผลิตวงจรรวม (IC manufacturing) และการบรรจุภัณฑ์และทดสอบวงจรรวม (IC packaging and testing)
บริษัทออกแบบวงจรรวมหลายแห่งเป็นบริษัทที่ไม่มีโรงงานผลิตเอง หรือที่เรียกว่า "fabless" ซึ่งหมายความว่าพวกเขาออกแบบและขายชิป แต่จ้างกระบวนการผลิตและทดสอบภายนอก บริษัท fabless ที่มีชื่อเสียงได้แก่ Qualcomm, NVIDIA, Broadcom รวมถึงบริษัทในไต้หวัน เช่น MediaTek, Novatek และ Realtek
การผลิตวงจรรวมดำเนินการโดยโรงหล่อชิป (Foundries) เช่น TSMC และ UMC จากไต้หวัน รวมถึง GlobalFoundries ส่วนการบรรจุภัณฑ์และการทดสอบวงจรรวมดำเนินการโดยบริษัท OSATs (Outsourced Semiconductor Assembly and Test) เช่น ASE และ SPIL จากไต้หวัน รวมถึง Amkor และ JCET
นอกจากนี้ยังมีบริษัทผู้ผลิตอุปกรณ์แบบครบวงจร (IDMs - Integrated Device Manufacturers) เช่น Intel, Samsung Electronics และ Texas Instruments ซึ่งเป็นบริษัทที่ออกแบบ ผลิต บรรจุภัณฑ์ และทดสอบชิปของตัวเอง โดยบริหารจัดการทุกส่วนของห่วงโซ่อุตสาหกรรมเซมิคอนดักเตอร์ด้วยความสามารถในการผลิตอย่างครบวงจร
1 ) อุตสาหกรรมเซมิคอนดักเตอร์ต้นน้ำ
ส่วนต้นน้ำของอุตสาหกรรมเซมิคอนดักเตอร์เน้นที่การออกแบบวงจรรวม (IC Design) ซึ่งบริษัทจะสร้างและตรวจสอบการทำงานของชิป โดยเปลี่ยนแนวคิดให้กลายเป็นการออกแบบชิป
- Memory ICs: ใช้สำหรับจัดเก็บข้อมูลและคำสั่งโปรแกรม พบได้ในพีซี สมาร์ทโฟน เครื่องเล่นเกม และกล้องดิจิทัล
- Micro Component ICs: รวมถึงหน่วยประมวลผลกลาง (CPU) และหน่วยประมวลผลกราฟิก (GPU) ที่ทำหน้าที่ประมวลผลข้อมูลและคำสั่ง ใช้ในสมาร์ทโฟน อิเล็กทรอนิกส์ยานยนต์ และเครื่องใช้ในบ้าน
- Logic ICs: ทำหน้าที่ประมวลผลทางตรรกะและควบคุมสัญญาณ ใช้ในอุปกรณ์สื่อสาร อิเล็กทรอนิกส์ยานยนต์ และระบบอัตโนมัติในอุตสาหกรรม
- Analog ICs: ประมวลผลสัญญาณแบบต่อเนื่อง เช่น แรงดันไฟฟ้าและกระแสไฟฟ้า ใช้ในอุปกรณ์เสียง การสื่อสารไร้สาย การจัดการพลังงาน และเซนเซอร์
2 )อุตสาหกรรมเซมิคอนดักเตอร์กลางน้ำ
เมื่อการออกแบบวงจรรวม (IC) เสร็จสิ้น กระบวนการจะเข้าสู่ขั้นตอนการผลิต ส่วนกลางของอุตสาหกรรมเซมิคอนดักเตอร์เกี่ยวข้องกับการผลิตและประมวลผลเวเฟอร์ ซึ่งเป็นขั้นตอนที่นำวงจรที่ออกแบบไว้มาสร้างบนเวเฟอร์เพื่อผลิตชิป (IC)
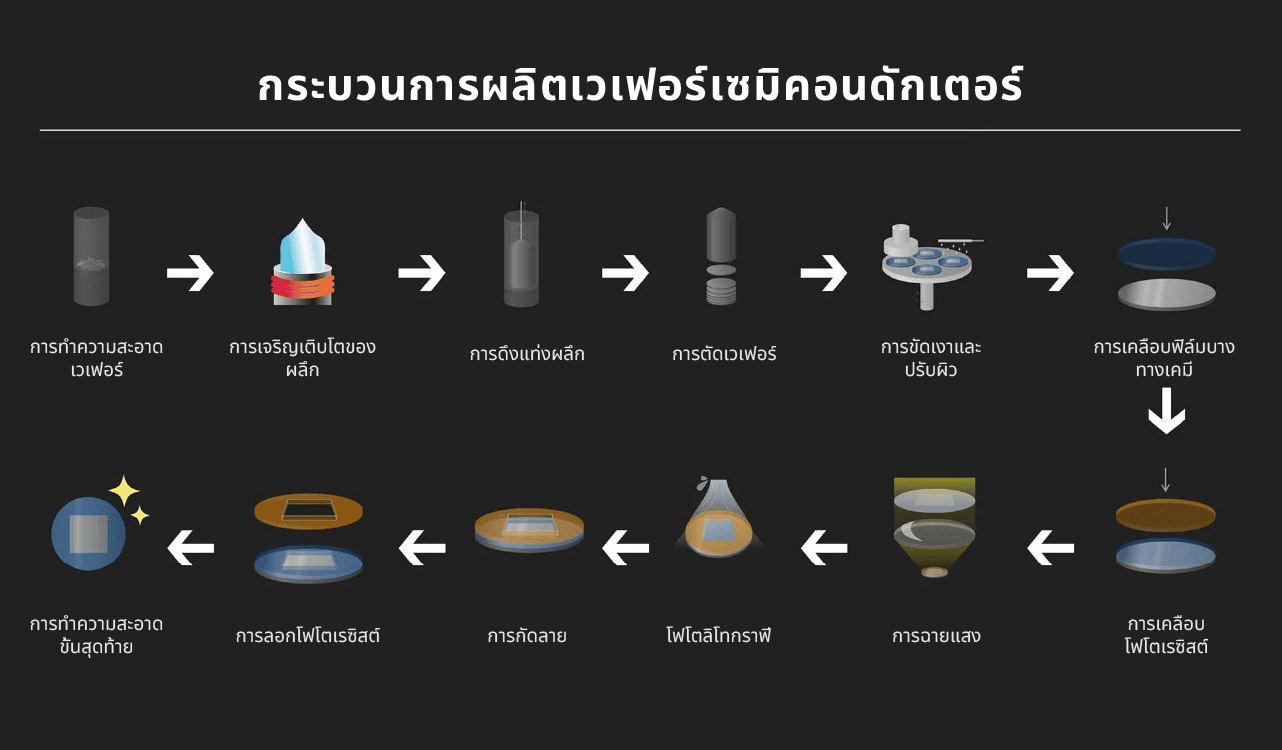
3 ) อุตสาหกรรมเซมิคอนดักเตอร์ปลายน้ำ
หลังจากการผลิตเวเฟอร์ ขั้นตอนถัดไปคือการตรวจสอบการทำงานของเวเฟอร์ ส่วนปลายน้ำของอุตสาหกรรมเซมิคอนดักเตอร์เกี่ยวข้องกับ การบรรจุภัณฑ์ (IC Packaging) และ การทดสอบ (IC Testing)
ในขั้นตอนการบรรจุภัณฑ์ เวเฟอร์ที่ผลิตจากกระบวนการผลิตจะถูกตัดออกเป็น IC Die แต่ละชิ้น จากนั้นจึงนำไปบรรจุในแพ็กเกจป้องกันที่ช่วยให้เชื่อมต่อทางไฟฟ้าได้ หลังจากบรรจุภัณฑ์เสร็จสิ้น จะเข้าสู่ขั้นตอนการทดสอบ IC เพื่อให้มั่นใจว่า IC ที่บรรจุไว้สามารถทำงานได้อย่างถูกต้องและตรงตามข้อกำหนดด้านประสิทธิภาพ
เมื่อผ่านขั้นตอนเหล่านี้แล้ว วงจรรวม (IC) จึงจะกลายเป็นผลิตภัณฑ์สำเร็จรูปพร้อมออกสู่ตลาดในรูปแบบของ ชิป
5. เวเฟอร์ถูกผลิตขึ้นอย่างไร?
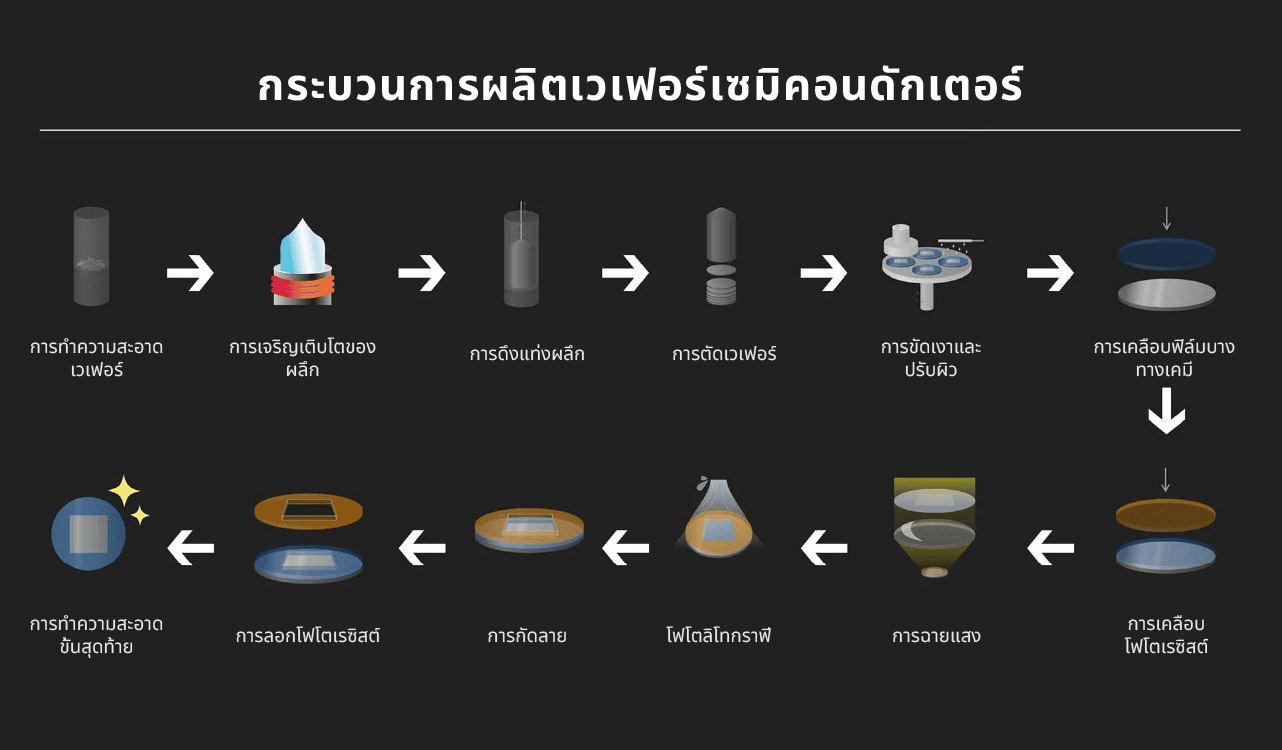
[6]
ความแตกต่างระหว่างเวเฟอร์และชิปคืออะไร? เวเฟอร์คือวัสดุเริ่มต้นในการผลิตชิป โดยเป็นแผ่นบางทรงกลมที่ทำจากซิลิกอนเดี่ยว (Single-Crystal Silicon) กระบวนการผลิตเวเฟอร์แบ่งออกเป็นสองขั้นตอนหลัก ขั้นตอนแรกประกอบด้วยการทำความสะอาดเวเฟอร์ การเจริญเติบโตของผลึก การดึงแท่งผลึก การตัดเวเฟอร์ และการขัดผิว ขั้นตอนที่สองเรียกว่า การผลิตเวเฟอร์ (Wafer Fabrication) ซึ่งรวมถึงกระบวนการต่าง ๆ เช่น การสะสมไอสาร (Vapor Deposition) การเคลือบสารไวแสง การฉายแสง การล้างลาย การกัดลาย การลอกสารไวแสง และการทำความสะอาดขั้นสุดท้าย
การทำความสะอาดเวเฟอร์
Wafer Cleaning
พื้นผิวของวัตถุดิบเวเฟอร์จะถูกทำความสะอาดด้วยการหลอมละลายที่อุณหภูมิสูงและการใช้สารละลาย เช่น กรดไฮโดรฟลูออริก (HF) หรือ โพแทสเซียมไฮดรอกไซด์ (KOH) เพื่อกำจัดสิ่งปนเปื้อนและสารอินทรีย์ตกค้าง เพื่อให้ได้คุณภาพของแผ่นเวเฟอร์ที่ดีเยี่ยม
การเจริญเติบโตของผลึก
Crystal Growth
วัตถุดิบซิลิกอนความบริสุทธิ์สูง ซิลิกอนไดออกไซด์ จะถูกนำเข้าสู่เตาหลอมเพื่อการกลั่นและลดรูปเป็น ซิลิกอนเกรดโลหกรรม (Metallurgical-Grade Silicon) หลังจากนั้นจะผ่านกระบวนการกลั่นด้วยการกลั่นแบบกลั่นลำดับส่วน (Distillation Purification) และกระบวนการสลายตัวอย่างช้า ๆ เพื่อผลิต ซิลิกอนแบบโพลีคริสตัลไลน์ (Polycrystalline Silicon)
การดึงแท่งผลึก
Ingot Pulling
ซิลิกอนโพลีคริสตัลไลน์จะถูกหลอมรวมกับกรดบอริกและฟอสฟอรัสในเบ้าหลอมควอตซ์ จากนั้นในอุณหภูมิสูง แท่งซิลิกอนผลึกเดี่ยว (Seed Crystal) จะถูกจุ่มลงในของเหลวและค่อย ๆ ดึงขึ้นพร้อมกับการหมุน ซิลิกอนจะยึดติดกับแท่งผลึกและแข็งตัวอย่างสม่ำเสมอจนกลายเป็นแท่งซิลิกอนผลึกเดี่ยวทรงกระบอก (Single Crystal Silicon Ingot)
การตัดเวเฟอร์
Wafer Slicing
แท่งผลึกที่เพิ่งผลิตออกมาจะมีพื้นผิวที่ไม่เรียบ จำเป็นต้องใช้เครื่องมือเพชรเกรดอุตสาหกรรมในการตัดแต่ง โดยเริ่มจากการตัดปลายที่เรียวออก ปรับขนาดเส้นผ่านศูนย์กลาง และตัดแท่งผลึกออกเป็นแผ่นเวเฟอร์บาง ๆ ด้วยใบเลื่อยหรือเลื่อยลวดที่มีความแข็งแรงสูง
การขัดเงาและการเจียระไน
Polishing & Lapping
หลังจากการตัดเวเฟอร์ พื้นผิวของเวเฟอร์จะมีความหยาบ ซึ่งต้องผ่านกระบวนการขัดเงาและเจียระไน การขัดเงาช่วยให้พื้นผิวผลึกเรียบและเงางามมากขึ้น ส่วนการเจียระไนช่วยปรับขอบเวเฟอร์ให้เป็นโค้งมนเรียบเพื่อป้องกันการแตกหัก
การสะสมไอสารเคมี
CVD (Chemical Vapor Deposition)
CVD (Chemical Vapor Deposition) เป็นกระบวนการที่นำแก๊สสารตั้งต้นเข้าสู่ห้องปฏิกิริยา เมื่อแก๊สเหล่านี้สัมผัสกับพื้นผิววัสดุที่ถูกทำให้ร้อน จะเกิดการสะสมของวัสดุเป็นชั้นฟิล์มบางบนพื้นผิว ใช้สำหรับสร้างชั้นฉนวนหรือชั้นนำไฟฟ้า
การเคลือบสารไวแสง
Photoresist Coating
เมื่อสัมผัสกับแสง สารไวแสง (Photoresist) จะเกิดการเปลี่ยนแปลงทางเคมี ขั้นตอนแรกคือการเคลือบสารไวแสงลงบนพื้นผิวเวเฟอร์อย่างสม่ำเสมอ เพื่อให้สามารถลอกออกหรือคงไว้ในขั้นตอนการฉายแสงและพัฒนาลวดลาย (Exposure and Development) เพื่อสร้างลวดลายที่ต้องการบนเวเฟอร์
การฉายแส
Exposure
ด้วยการใช้ลวดลายบน โฟโตมาสก์ (Photomask) ทำการฉายแสงอัลตราไวโอเลตลงบนชั้นสารไวแสง จัดแนวโฟโตมาสก์ให้ตรงกับเวเฟอร์ที่เคลือบสารไวแสง เมื่อแสงส่องลงไปบนบริเวณที่ต้องการ จะกระตุ้นให้เกิดปฏิกิริยาเคมีในชั้นสารไวแสงในพื้นที่ที่ได้รับแสง ทำให้เกิด ปฏิกิริยาทางแสงเคมี (Photochemical Reaction)
การถ่ายโอนลวดลายด้วยแสง
Photolithography
เวเฟอร์จะถูกนำไปสัมผัสกับสารละลายสำหรับการพัฒนา (Developing Solution) ซึ่งอาจมีส่วนผสมของด่าง เช่น โซเดียมไฮดรอกไซด์ (NaOH) หรือ โพแทสเซียมไฮดรอกไซด์ (KOH) พร้อมสารเติมแต่ง สารละลายนี้จะลบชั้นสารไวแสงในบริเวณที่ไม่ได้รับแสงออกไป ทำให้บริเวณที่ได้รับแสงคงอยู่ และสร้างลวดลายตามที่ต้องการบนเวเฟอร์
การกัดลาย
Etching
โดยใช้สารละลายกรดหรือด่างในการกัดลายวัสดุที่อยู่ใต้ชั้นสารไวแสง ตามลวดลายที่กำหนดไว้บนชั้นสารไวแสง พื้นที่ที่ได้รับการปกป้อง (บริเวณที่สารไวแสงยังคงอยู่) จะไม่ได้รับผลกระทบ กระบวนการนี้ช่วยสร้างโครงสร้างจุลภาคบนพื้นผิวเวเฟอร์ ซึ่งเป็นขั้นตอนสำคัญในการขึ้นรูปชิป
การลอกสารไวแสง
Photoresist Stripping
หลังจากขั้นตอนการพัฒนา สารไวแสงที่ตกค้างจะถูกลอกออกโดยใช้วิธีการทางเคมี ความร้อน หรือเชิงกล เช่น การใช้สารละลายลอกสารไวแสง เพื่อป้องกันผลกระทบที่อาจส่งผลต่อประสิทธิภาพการทำงานของอุปกรณ์
การทำความสะอาดขั้นสุดท้าย
(Final Cleaning)
สุดท้าย ชิปจะเข้าสู่กระบวนการทำความสะอาดครั้งที่สอง ซึ่งอาจใช้ตัวทำละลายอินทรีย์หรืออนินทรีย์ สารลดแรงตึงผิว หรือเทคนิคการทำความสะอาดด้วยอัลตราโซนิก เพื่อลบคราบสารเคมีและอนุภาคที่ตกค้างจากกระบวนการผลิต เพื่อให้มั่นใจว่าชิปที่ผลิตได้สะอาดและเป็นไปตามข้อกำหนด
การประยุกต์ใช้งานของเครื่องวัดการไหลและหัวฉีดในอุตสาหกรรมเซมิคอนดักเตอร์
การประยุกต์ใช้งานที่ 1: การตรวจวัดการไหลของสารเคมี
ในกระบวนการผลิตเซมิคอนดักเตอร์ การควบคุมการไหลของสารเคมีเหลวอย่างแม่นยำถือเป็นสิ่งสำคัญ เนื่องจากกระบวนการผลิตมีความซับซ้อนและละเอียดอ่อน ทุกขั้นตอนในการผลิตขึ้นอยู่กับการจ่ายสารเคมีที่แม่นยำและการควบคุมอัตราการไหลที่เหมาะสม ซึ่งส่งผลต่อคุณภาพและเสถียรภาพของผลิตภัณฑ์ เครื่องวัดการไหลของของเหลวจึงมีบทบาทสำคัญในการควบคุมและตรวจสอบการไหลของของเหลวภายในท่ออย่างแม่นยำ เพื่อรับประกันคุณภาพและประสิทธิภาพของผลิตภัณฑ์
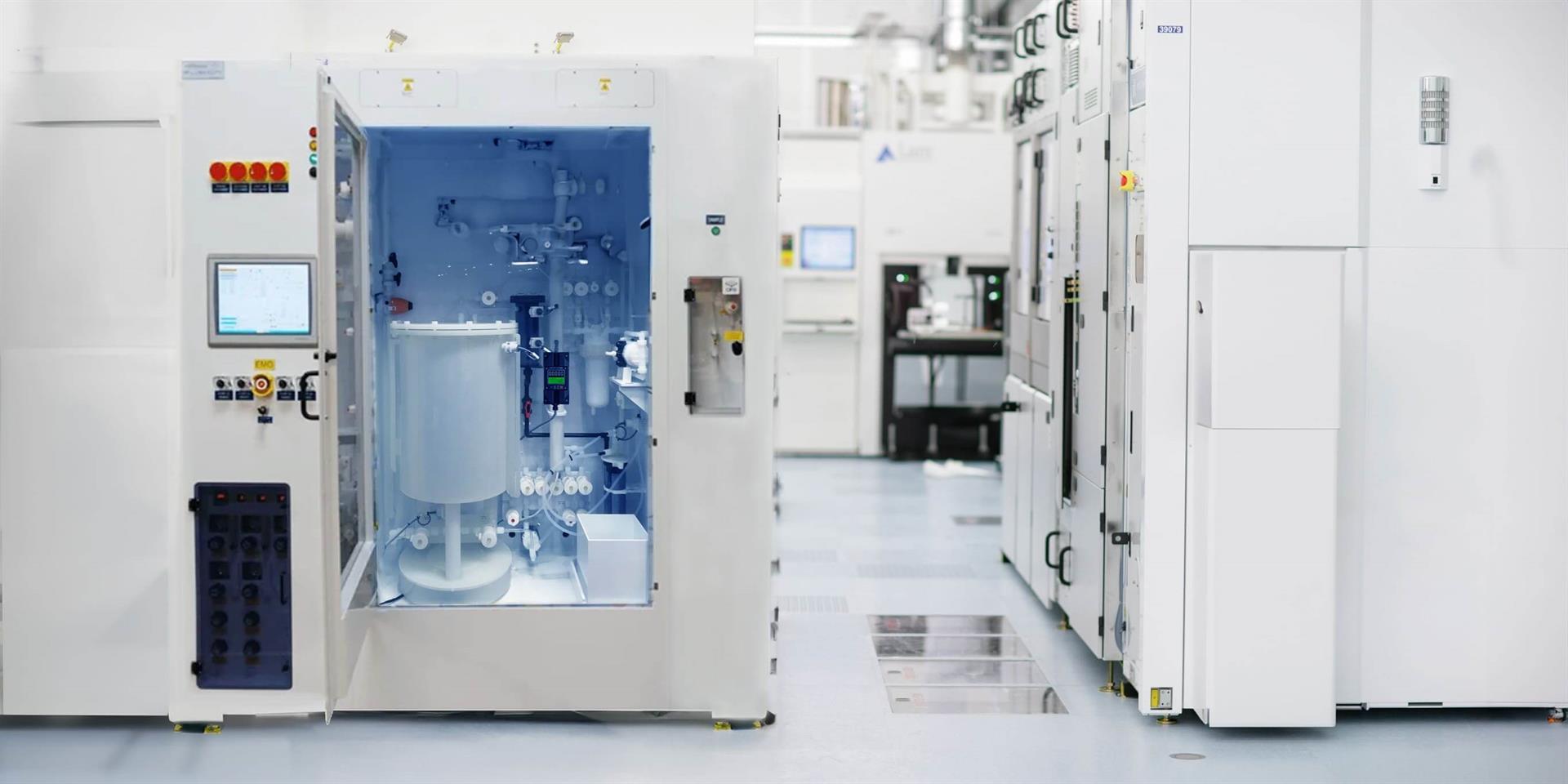
กรณีศึกษา: โรงงานเซมิคอนดักเตอร์เทคโนโลยีจีน
สถานการณ์: โรงงานแบบดั้งเดิมที่ไม่มีระบบจ่ายสารเคมีจากศูนย์กลาง มักจะขนส่งสารเคมีแต่ละชนิดแยกกันไปยังพื้นที่และอุปกรณ์ต่างๆ การดำเนินการในลักษณะนี้อาจก่อให้เกิดความเสี่ยงด้านความปลอดภัยและส่งผลให้เกิดความไม่มีประสิทธิภาพในการใช้สารเคมีให้เกิดประโยชน์สูงสุด
โซลูชัน: LORRIC FP-AS510 Paddlewheel Flow Meter
เพื่อแก้ไขปัญหานี้ เราแนะนำให้จัดตั้งห้องเก็บสารเคมีส่วนกลางภายในโรงงานของบริษัท โดยระหว่างการดำเนินงาน สารเคมีจะถูกส่งไปยังแต่ละเครื่องจักรจากศูนย์กลาง และเครื่องวัดอัตราการไหลแบบพัดลม FP-AS510 จะถูกใช้ในการคำนวณปริมาณที่ต้องการอย่างแม่นยำ เพื่อลดต้นทุนการสูญเสียสารเคมีระหว่างกระบวนการ เครื่องวัดอัตราการไหล FP-AS510 ซึ่งถือครองสิทธิบัตรและการรับรองระดับสากลหลายรายการ มาพร้อมกับเทคโนโลยีสิทธิบัตร AxleSense โครงสร้างใบพัดแบบล้อน้ำช่วยตรวจจับการไหลที่เล็กมากเมื่อของไหลผ่านไป ทำให้สามารถวัดปริมาณของเหลวได้อย่างแม่นยำ FP-AS510 ยังมีความสามารถในการตรวจสอบแบบเรียลไทม์สำหรับสภาพใบพัดที่ผิดปกติ โดยตรวจจับปัญหาการไหลเป็นศูนย์ที่เกิดจากการหายไปของใบพัดได้
ด้วยการติดตั้ง FP-AS510 บริษัทสามารถคำนวณปริมาณสารเคมีที่แต่ละเครื่องต้องการในระหว่างการเตรียมสารเคมีได้อย่างแม่นยำ ส่งผลให้เกิดการประหยัดต้นทุน นอกจากนี้ เนื่องจากสารเคมีมีความเข้มข้นสูงและมีฤทธิ์กัดกร่อน ซึ่งอาจก่อให้เกิดความเสี่ยงระหว่างการจัดเก็บและการขนส่ง การใช้ FP-AS510 จะช่วยลดความเสี่ยงนี้ได้ ผลิตภัณฑ์นี้ทำจากวัสดุ PVDF ซึ่งมีความทนทานต่อสารทำละลายและการกัดกร่อนจากกรด-ด่างได้อย่างดีเยี่ยม ช่วยขจัดความกังวลเรื่องการกัดกร่อนและการรั่วไหลของสารเคมี พร้อมเพิ่มความปลอดภัยในสถานที่ทำงาน
การประยุกต์ใช้งานที่ 2: การวัดและการตรวจสอบน้ำบริสุทธิ์พิเศษ (Ultra-Pure Water)
ในกระบวนการผลิตเซมิคอนดักเตอร์ น้ำบริสุทธิ์พิเศษถูกใช้อย่างมากในขั้นตอนต่างๆ เช่น การทำความสะอาดเวเฟอร์ การล้างชิ้นส่วนอิเล็กทรอนิกส์ และกระบวนการกัดเซาะ (etching) ในกระบวนการบำบัดน้ำบริสุทธิ์พิเศษ การวัดปริมาณการไหลของของเหลวอย่างแม่นยำเป็นสิ่งจำเป็น
ตัวอย่างเช่น ในกระบวนการรีเวิร์สออสโมซิส (RO) การวัดอัตราการไหลของน้ำเข้มข้น (concentrate) เป็นสิ่งสำคัญเพื่อควบคุมอัตราส่วนความเข้มข้นและป้องกันการเกิดตะกรันบนเมมเบรน การตรวจสอบการไหลของน้ำอย่างต่อเนื่องยังช่วยประเมินประสิทธิภาพของอุปกรณ์ RO เพื่อระบุความผิดปกติหรือปัญหาที่อาจเกิดขึ้นได้ทันที
ในกระบวนการกำจัดไอออน (Deionization หรือ DI) จะใช้เรซินแลกเปลี่ยนไอออนเพื่อกำจัดไอออนออกจากน้ำ ซึ่งต้องตรวจสอบอัตราการไหลของน้ำผ่านเรซิน และการไหลของน้ำล้างกลับ (backwash) เพื่อให้มั่นใจว่ากระบวนการกำจัดไอออนมีประสิทธิภาพ
นอกจากนี้ ในขั้นตอนการเติมสารเคมีเพื่อบำบัดน้ำบริสุทธิ์พิเศษ การควบคุมปริมาณสารเคมีอย่างแม่นยำก็มีความสำคัญ เช่น การวัดปริมาณสารฆ่าเชื้อ (คลอรีน คลอรีนไดออกไซด์ โอโซน) เพื่อกำจัดจุลชีพ หรือการวัดสารปรับค่า pH (กรดซัลฟิวริก โซเดียมไฮดรอกไซด์) เพื่อรักษาเสถียรภาพของคุณภาพน้ำ
ดังนั้น การบำบัดน้ำบริสุทธิ์พิเศษจึงต้องการเครื่องมือวัดการไหลของของเหลวที่มีความแม่นยำสูง และต้องมีความทนทานต่อสารเคมี
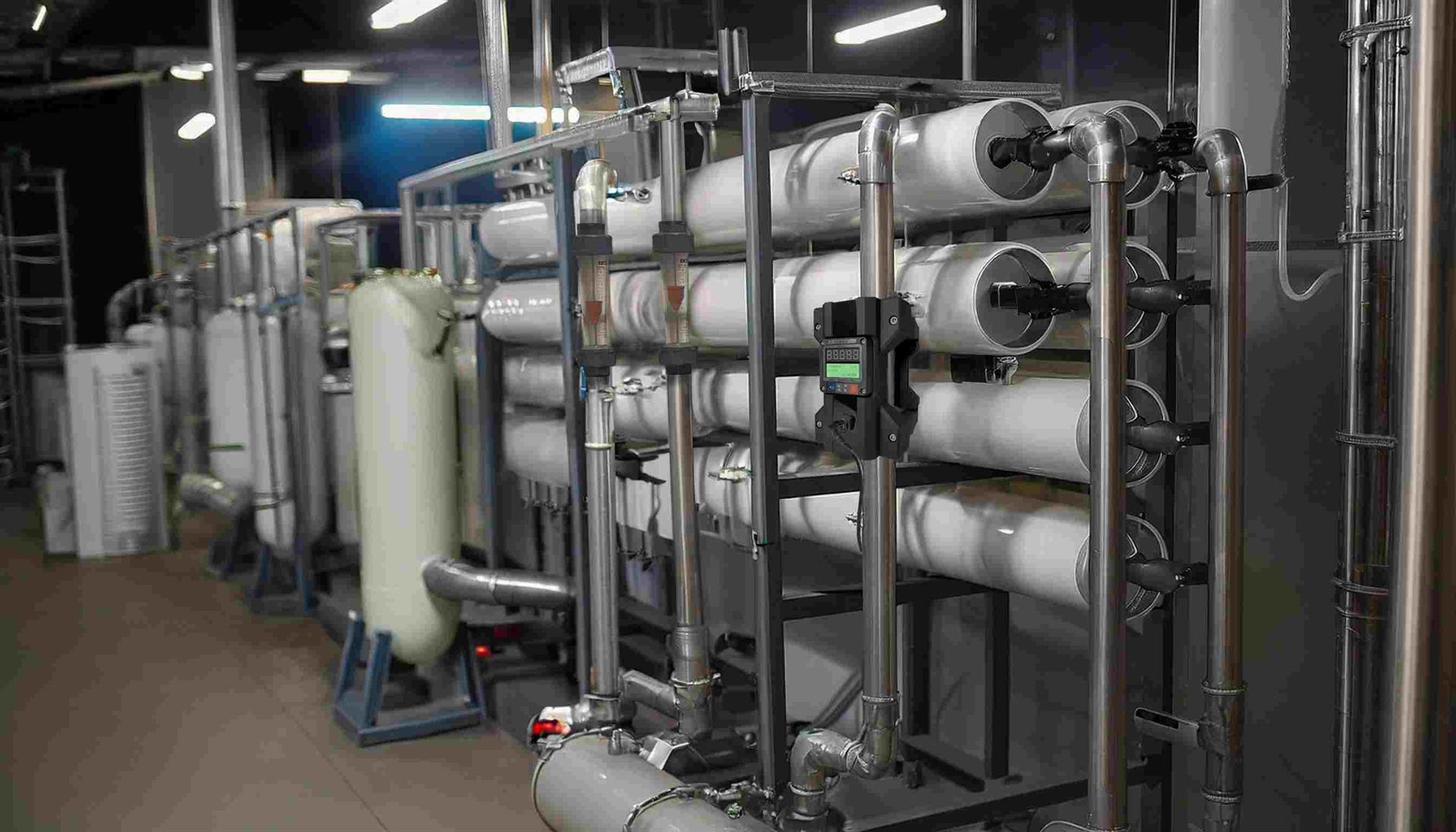
กรณีศึกษา: โรงงานเซมิคอนดักเตอร์ชั้นนำของไต้หวัน
สถานการณ์: บริษัทนี้เชี่ยวชาญในการออกแบบระบบบำบัดน้ำ เช่น ระบบน้ำบริสุทธิ์พิเศษ ระบบรีไซเคิลน้ำเสีย และโครงการบำบัดน้ำเสีย ในกระบวนการบำบัดน้ำบริสุทธิ์พิเศษ ไม่สามารถใช้เครื่องวัดการไหลแบบแม่เหล็กไฟฟ้ามาตรฐานได้ เนื่องจากน้ำบริสุทธิ์พิเศษเป็นน้ำที่ไม่สามารถนำไฟฟ้าได้
บริษัทจึงมองหาการแก้ปัญหาด้วยเครื่องวัดการไหลแบบอัลตราโซนิก แต่รุ่นทั่วไปในตลาดมีขั้นตอนการติดตั้งและตั้งค่าที่ยุ่งยากและซับซ้อน นอกจากนี้ยังต้องเติมเจลอัลตราโซนิกเป็นประจำ ซึ่งส่งผลให้ประสบการณ์การใช้งานไม่เป็นที่น่าพอใจ
นอกจากนี้ บริษัทยังต้องการการแก้ปัญหาที่สามารถวัดการไหลของของเหลวขนาดเล็กได้อย่างแม่นยำ และสามารถทนทานต่อสารเคมีได้ดีในระหว่างกระบวนการบำบัดน้ำบริสุทธิ์พิเศษ
โซลูชัน: LORRIC's Ultrasonic Flow Meters
เราขอแนะนำให้ติดตั้งเครื่องวัดการไหลแบบอัลตราโซนิกของ LORRIC ในอุปกรณ์การบำบัดน้ำบริสุทธิ์ของบริษัท เครื่องวัดนี้ติดตั้งง่าย การวัดการไหลสองทิศทางช่วยขจัดข้อกังวลเรื่องทิศทางการไหล มีระบบติดตามหัววัดที่ได้รับสิทธิบัตรเพื่อการวางตำแหน่งที่แม่นยำ และอุปกรณ์ยึดที่ช่วยให้การติดตั้งมั่นคง ซึ่งช่วยเพิ่มความแม่นยำของการไหล รับประกันความเสถียร และอนุญาตให้ถอดและบำรุงรักษาได้โดยไม่ทำลายกระบวนการ ซึ่งทำให้การติดตั้งสะดวกยิ่งขึ้น เครื่องวัดการไหลแบบอัลตราโซนิกของ LORRIC ใช้เซนเซอร์สองตัวในการวัดความถี่ของคลื่นอัลตราโซนิก คำนวณความเร็วการไหลที่แม่นยำ เหมาะสำหรับระบบ RO, การตรวจสอบน้ำความเข้มข้นสูงผ่านเยื่อกรองอัลตราฟิลเตรชันเพื่อความเสถียร และกระบวนการ DI เพื่อเพิ่มประสิทธิภาพในการกำจัดไอออนผ่านเรซินแลกเปลี่ยนไอออน เครื่องวัดเหล่านี้มีความทนทานต่อสารเคมีได้ดี ตอบสนองต่อข้อกำหนดเฉพาะ
การประยุกต์ใช้งานที่ 3: หัวฉีดแบบเกลียว - ส่วนประกอบหลักในกระบวนการบำบัดก๊าซไอเสียเซมิคอนดักเตอร์
ในกระบวนการผลิตเซมิคอนดักเตอร์ ก๊าซที่เป็นอันตราย (เช่น แอมโมเนีย ซัลเฟอร์ไดออกไซด์ ไนโตรเจนไดออกไซด์ กรดไฮโดรฟลูออริก ฯลฯ) จะถูกปล่อยออกมาเป็นก๊าซไอเสีย ดังนั้น หัวฉีดแบบเกลียวจึงถูกใช้ในหอการบำบัดก๊าซไอเสียเพื่อพ่นสารล้างเช่น สารละลายด่าง (โซเดียมไฮดรอกไซด์) เพื่อทำให้ก๊าซกรด (แอมโมเนีย) เป็นกลาง หรือสารละลายกรด (กรดไฮโดรฟลูออริก) เพื่อทำให้ก๊าซด่าง (โซเดียมไฮดรอกไซด์, แอมโมเนียมไฮดรอกไซด์) เป็นกลาง
กระบวนการนี้ช่วยเปลี่ยนสารอันตรายให้กลายเป็นสารประกอบที่มั่นคงและสามารถจัดการได้ ทำให้ก๊าซไอเสียที่ปล่อยออกมาจากโรงงานได้รับการบำบัดอย่างมีประสิทธิภาพ และช่วยให้สอดคล้องกับข้อกำหนดในการบำบัดก๊าซไอเสีย นอกจากนี้ยังส่งเสริมเป้าหมายการพัฒนาที่ยั่งยืน
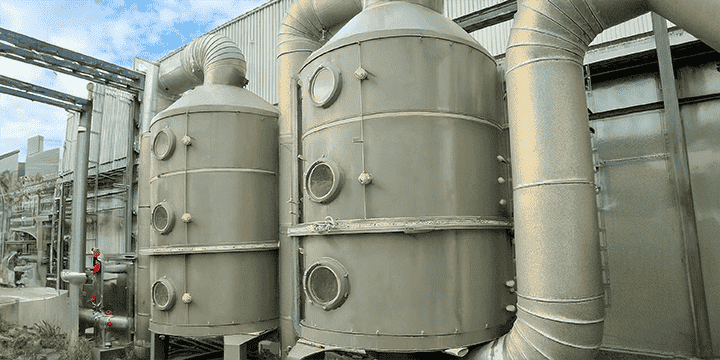
กรณีศึกษา: โรงงานผลิตเวเฟอร์ชั้นนำของไต้หวัน
สถานการณ์: หัวฉีดจากแบรนด์หลักส่วนใหญ่ผลิตโดยการฉีดขึ้นรูปพลาสติก ซึ่งสร้างโมเดลหัวฉีดโดยตรงจากแม่พิมพ์ วิธีการผลิตนี้จำกัดความสามารถของหัวฉีดแบบเกลียวในการมีผิวเกลียวที่มีความแม่นยำสูงและช่องทางทรงกรวย ซึ่งส่งผลให้พื้นที่การพ่นน้ำลดลงและประสิทธิภาพการทำงานน้อยลง นอกจากนี้ หัวฉีดทั่วไปมักใช้วัสดุ PP (โพลีโพรพีลีน) ซึ่งขาดความแข็งแรงและความแข็ง ตัววัสดุนี้เปราะแตกง่ายและทนทานต่อสภาพแวดล้อมที่มีสารเคมีอุณหภูมิสูงได้จำกัด
หัวฉีดเหล่านี้ไม่เพียงแค่ไม่สามารถทำให้การกระจายของน้ำได้ครอบคลุมอย่างมีประสิทธิภาพ แต่ยังขาดความทนทานต่อการกัดกร่อนที่จำเป็นสำหรับการบำบัดของเสียในอุตสาหกรรมเซมิคอนดักเตอร์
โซลูชัน: หัวฉีดแบบเกลียว LORRIC
หัวฉีดแบบเกลียวของ LORRIC ผลิตด้วยกระบวนการแมชีนที่มีความแม่นยำสูง โดยการแกะสลักวัสดุให้เป็นหัวฉีดทรงเกลียวแบบกรวยแข็ง รูปแบบของช่องทางการไหลที่ใหญ่กว่าช่วยป้องกันการอุดตันจากสิ่งสกปรกได้อย่างมีประสิทธิภาพ และพื้นที่การพ่นน้ำมีขนาดใหญ่กว่าหัวฉีดจากแบรนด์อื่นในตลาด โดยมีมุมการพ่นได้สูงสุดถึง 170 องศา นอกจากนี้ หัวฉีดแบบเกลียวของ LORRIC ผลิตจากวัสดุทนการกัดกร่อนระดับสูง - UPVC (โพลีไวนิลคลอไรด์) และ PEEK (โพลีอีเธอร์อีเธอร์คีโตน) ซึ่งช่วยยืดอายุการใช้งานของหัวฉีดในสภาพแวดล้อมที่มีสารเคมีที่มีปฏิกิริยาสูง พวกมันจึงเป็นตัวเลือกที่ดีที่สุดสำหรับการบำบัดก๊าซไอเสียในอุตสาหกรรมการผลิตเซมิคอนดักเตอร์