1. Cấu trúc Thép Khả năng Cứng sau Gia nhiệt của Ô tô
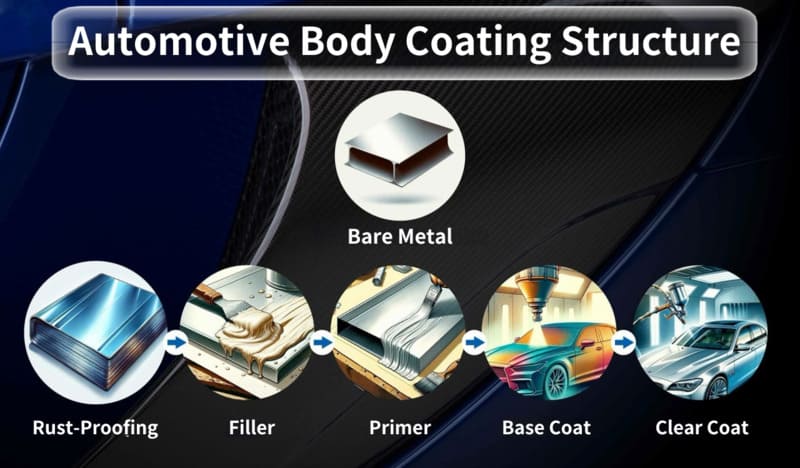
Để chọn đúng loại sơn cho sơn ô tô, điều quan trọng là phải hiểu cấu trúc và kỹ thuật cơ bản liên quan. Nền tảng của một lớp sơn ô tô là lớp dưới cùng, thường gọi là kim loại trần. Sau khi rời khỏi nhà máy, kim loại trần này trải qua quá trình làm sạch và tiền xử lý. Tiếp theo, một lớp chống rỉ được phủ lên để ngăn ngừa sự ăn mòn của kim loại. Một lớp làm phẳng cũng được sử dụng để làm mịn bề mặt.
Sau đó là lớp sơn lót, đóng vai trò là lớp bảo vệ cho kim loại và tạo bề mặt bám dính tốt cho các lớp tiếp theo. Tiếp theo lớp sơn lót là lớp màu chính, còn gọi là lớp sơn nền. Lớp này có thể bao gồm nhiều lớp để đảm bảo phân bố màu đồng đều. Cuối cùng, một lớp sơn bóng được phủ lên trên để tăng độ bóng và bảo vệ lớp sơn nền.
Sơn thân xe ô tô từ nhà máy đảm bảo chất lượng, do đó, nhiều người bán xe cũ nhấn mạnh sơn nguyên bản từ nhà máy, gián tiếp cho thấy xe không bị sửa chữa hoặc tai nạn lớn.
Trong sơn xe hiện đại, có nhiều loại sơn khác nhau được sử dụng, bao gồm men polyurethane acrylic với sơn lót, lớp sơn nền và lớp sơn bóng. Quy trình sơn đã tiến bộ theo thời gian, chuyển từ sơn thủ công cần vài tuần để khô sang phương pháp hiện đại, nơi nhiều lớp có thể khô trong vài giờ. Hiểu các loại sơn ô tô khác nhau, như hệ thống sơn gốc nước và sơn gốc dung môi, là điều quan trọng để đạt được kết quả mong muốn và tuân thủ các yêu cầu về môi trường.
[1]
2. Chọn Đúng Loại Sơn - Các Loại Sơn Khác Nhau
Khi chọn sơn cho thân xe ô tô, điều quan trọng là xem xét loại sơn, những ưu nhược điểm của nó, và cách đánh giá tính chuyên nghiệp của các cửa hàng sơn. Dưới đây là hướng dẫn toàn diện:
Sơn Men Polyurethane Acrylic: Hầu hết các xe hiện đại sử dụng loại sơn này, bao gồm sơn lót, lớp sơn nền và lớp sơn bóng. Nó cung cấp độ bền tuyệt vời và bề mặt hoàn thiện chất lượng cao.
Sơn Laquer: Từng là lựa chọn phổ biến, sơn laquer giờ đây ít được ưa chuộng hơn do sự phát triển của các loại sơn khác mang lại độ bóng và bảo vệ bề mặt tốt hơn. Tuy nhiên, nó có thể vẫn được sử dụng để phục hồi xe cổ về trạng thái nguyên bản.
Sơn Một Giai Đoạn: Loại sơn này kết hợp màu và độ bóng trong một công thức và thường được sử dụng cho xe thương mại và xe tải. Nó dễ áp dụng hơn nhưng có thể cung cấp độ sâu ít hơn trong lớp hoàn thiện so với các hệ thống đa giai đoạn.
Sơn Lớp Nền và Lớp Bóng: Hệ thống hai giai đoạn bao gồm lớp sơn nền màu được theo sau bởi lớp sơn bóng. Nó cung cấp độ bóng sâu hơn và bảo vệ tốt hơn nhưng phức tạp hơn trong việc áp dụng.
Sơn Tri-Coat hoặc Đa Giai Đoạn: Chủ yếu được sử dụng cho các xe cao cấp, hệ thống này bắt đầu bằng lớp sơn nền, thêm một lớp giữa với hạt ngọc hoặc phụ gia, và hoàn thiện bằng lớp sơn bóng để tăng cường độ sâu và độ bóng.
Hệ Thống Sơn Gốc Nước và Gốc Dung Môi: Sơn gốc nước thân thiện với môi trường và ngày càng được ưa chuộng. Hệ thống gốc dung môi là truyền thống nhưng chứa các hợp chất hữu cơ dễ bay hơi (VOCs), gây lo ngại về môi trường và sức khỏe.
[2]
1 ) Chọn Đúng Loại Sơn - Những Lưu Ý Quan Trọng
Loại Xe và Mục Đích Sử Dụng: Lựa chọn sơn phụ thuộc vào loại xe và mục đích sử dụng. Ví dụ, xe thương mại có thể phù hợp với sơn một giai đoạn, trong khi xe sang trọng có thể cần sơn ba lớp để có lớp hoàn thiện tinh tế hơn.
Tác Động Môi Trường: Xem xét các tùy chọn thân thiện với môi trường như sơn gốc nước, đặc biệt ở những khu vực mà sơn gốc dung môi bị hạn chế do hàm lượng VOC cao.
Lớp Hoàn Thiện Mong Muốn: Nếu bạn muốn có một lớp hoàn thiện sâu và bóng bẩy, các loại sơn đa giai đoạn như lớp sơn nền và lớp bóng hoặc hệ thống ba lớp là lý tưởng. Đối với lớp hoàn thiện đơn giản hơn, sơn một giai đoạn có thể là đủ.
2 ) Chọn Đúng Loại Sơn - Tính Chuyên Nghiệp Của Cửa Hàng Sơn
Chất Lượng Vật Liệu: Các cửa hàng chuyên nghiệp nên sử dụng sơn chất lượng cao được thiết kế dành riêng cho ô tô, như các sản phẩm do các nhà sản xuất như SYBON cung cấp, chuyên về nhiều loại sơn và lớp phủ ô tô.
Chuyên Môn Kỹ Thuật: Tìm kiếm các cửa hàng hiểu biết về nghệ thuật và khoa học trong sơn thân xe, bao gồm hóa học sơn, chuẩn bị bề mặt, kỹ thuật ứng dụng và hoàn thiện.
Tùy Chỉnh và Phối Màu: Một cửa hàng chuyên nghiệp nên cung cấp nhiều tùy chọn màu sắc và có công nghệ để phối màu chính xác, đảm bảo sự hòa hợp với lớp sơn hiện có.
Hướng Dẫn Bảo Trì và Độ Bền: Cửa hàng nên cung cấp hướng dẫn về cách duy trì lớp sơn, bao gồm việc rửa xe thường xuyên và áp dụng sáp hoặc chất chống thấm bảo vệ.
Tính Minh Bạch Trong Quy Trình: Một cửa hàng uy tín sẽ giải thích rõ ràng quy trình sơn của họ, từng bước một, như đã được Orlando Autobody nêu rõ, bao gồm xác định loại sơn, phối màu, chuẩn bị bề mặt, đánh bóng, sơn lót và hoàn thiện.
[3]
3. Chất Lượng Phun Cũng Ảnh Hưởng Đến Kết Quả Sơn
Trước khi sơn, xe ô tô trải qua quá trình tiền xử lý phun, trong đó chúng được làm sạch từ mọi góc độ bằng các vòi phun được lắp đặt ở cả hai bên của đường ray. Quá trình này đòi hỏi các vòi phun dễ dàng lắp đặt với số lượng lớn, có thể điều chỉnh hướng phun và dễ bảo trì.
Các vòi phun thông thường thường thiếu độ chính xác, dẫn đến phun không đều và chất lượng sơn kém. Vòi phun kẹp của LORRIC được kiểm tra tại nhà máy với độ chính xác trong phạm vi 10%, có thể điều chỉnh hướng phun và dễ dàng vệ sinh và bảo trì, đảm bảo lớp sơn đồng nhất.
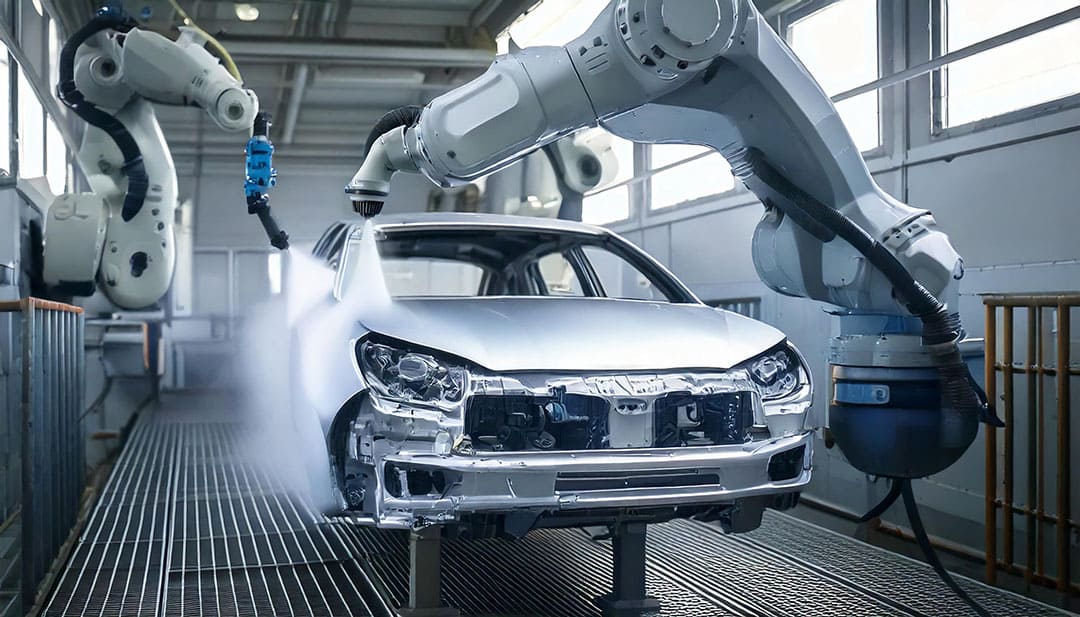
Trường hợp: Nhà cung cấp thiết bị sơn địa phương tại Đài Loan
Nhà sản xuất này chuyên cung cấp các loại thiết bị sơn tự động cho các vật liệu như sắt, nhôm, PVC và các vật liệu khác. Họ cung cấp các giải pháp tiền xử lý, phòng tẩy sơn và buồng sơn. Từ những năm 1990, họ đã trở thành nhà cung cấp thiết bị sơn hàng đầu cho nhiều thương hiệu quốc tế và ngành công nghiệp tại Đài Loan. Hợp tác của họ với LORRIC đã kéo dài hơn hai mươi năm.
Giải pháp: Vòi phun Kẹp của LORRIC
Vòi phun kẹp bao gồm cấu trúc ba phần, bao gồm vòi phun, đế và đai ốc. Chúng dễ dàng lắp đặt mà không cần dụng cụ, cho phép điều chỉnh hướng phun và thuận tiện cho việc bảo trì và vệ sinh, giảm chi phí thay thế vòi phun. Thêm vào đó, với hơn 30 năm kinh nghiệm sản xuất vòi phun, vòi phun của LORRIC cung cấp sự phân phối phun đồng nhất và đều đặn, vượt trội hơn so với các vòi phun thông thường về chất lượng và nâng cao hiệu suất máy móc cho người dùng cuối.