Tổng quan
- Mạ điện là kỹ thuật xử lý bề mặt kim loại phổ biến, cung cấp lớp bảo vệ, trang trí và cải thiện độ dẫn điện, nhưng có thể sinh ra hóa chất độc hại.
- Quy trình mạ điện gắn ion kim loại vào bề mặt qua điện phân, với cực dương, cực âm và chất điện phân, sử dụng các kim loại khác nhau cho các mục đích khác nhau.
- Phương pháp mạ đa dạng, gồm mạ rack, thùng và tầng sôi, phù hợp cho từng loại bộ phận và yêu cầu, giúp đảm bảo chất lượng sản phẩm.
- Lưu lượng kế (flow meter) và vòi phun kiểm soát chính xác lượng hóa chất, phân bố và thời gian tiếp xúc, ảnh hưởng đến chất lượng lớp mạ.
Tại sao cần mạ điện? Ưu và nhược điểm của mạ điện:
Mạ điện, được sử dụng rộng rãi trong các ngành điện tử, ô tô, hàng không vũ trụ và hóa chất, liên quan đến các phản ứng điện hóa để phủ lớp kim loại hoặc hợp kim lên bề mặt vật liệu, nhằm tăng tính thẩm mỹ, cải thiện độ dẫn điện, độ cứng và sửa chữa các khuyết điểm bề mặt. Các phương pháp mạ bao gồm mạ khối, mạ rack, mạ liên tục và mạ dây chuyền, phù hợp cho nhiều loại bộ phận khác nhau.
Lợi ích của mạ điện bao gồm cải thiện các tính chất vật lý, cơ học và hóa học của sản phẩm mạ. Tuy nhiên, quy trình phức tạp này có thể gặp các khuyết điểm như rỗ bề mặt và mất độ bám dính. Các vấn đề về môi trường cũng phát sinh do hóa chất độc hại được tạo ra trong quá trình này.
[1][2][3]
Nguyên lý và các loại mạ điện
Nguyên lý mạ điện
Quá trình mạ điện liên quan đến quá trình điện phân, trong đó các ion kim loại trong dung dịch điện phân được lắng đọng lên bề mặt vật liệu để tạo thành lớp mạ. Trong quá trình này, có ba thành phần chính: cực dương (kim loại dùng để mạ), cực âm (vật cần được mạ) và điện phân (dung dịch mạ).
Cực dương là một miếng kim loại cung cấp kim loại cho lớp mạ, trong khi cực âm là vật cần được mạ. Dung dịch điện phân thường bao gồm dung dịch chứa các cation của kim loại phủ, ion phi kim và các thành phần hóa học khác.
Khi có dòng điện, các cation kim loại trong dung dịch điện phân di chuyển đến cực âm, tại đây chúng nhận electron và chuyển thành kim loại, bám vào bề mặt vật liệu. Đồng thời, kim loại ở cực dương hòa tan (bị oxy hóa), cung cấp thêm ion kim loại cho dung dịch điện phân. Theo thời gian, một lớp phim kim loại mỏng được hình thành trên bề mặt vật liệu được mạ.
Các loại mạ điện
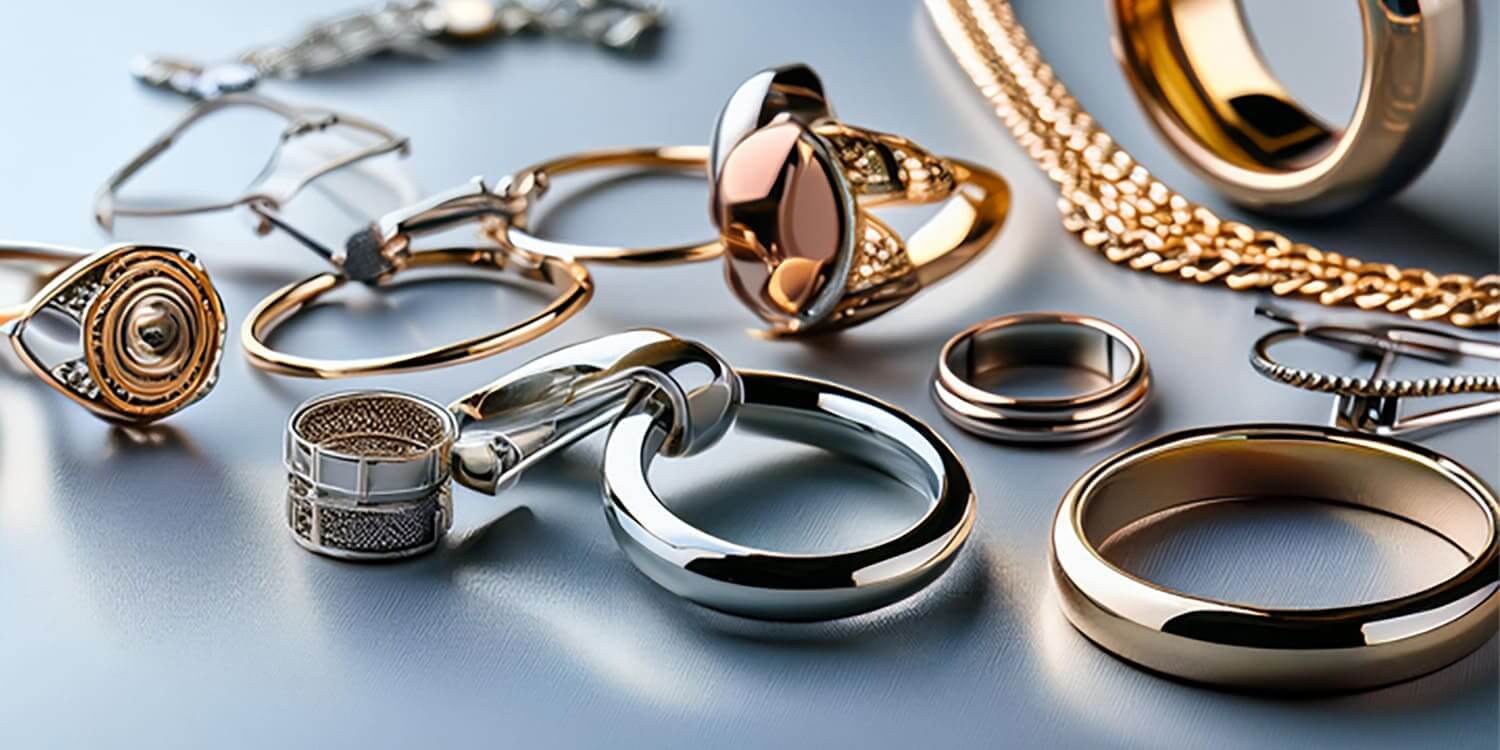
Các kim loại khác nhau được sử dụng cho mạ điện cung cấp các mức độ cứng khác nhau, ảnh hưởng đến khả năng chống mài mòn và chống ăn mòn. Việc lựa chọn kim loại để phủ trang trí phụ thuộc vào vẻ ngoài mong muốn. Đối với các thành phần điện tử, độ dẫn điện là một yếu tố quan trọng. Phân loại mạ điện theo kim loại bao gồm:
Mạ điện trang trí: Loại này bao gồm mạ đồng, niken, crom, v.v., nhằm tăng độ mịn và vẻ đẹp thẩm mỹ của bề mặt sản phẩm. Lớp kim loại thường có độ bóng cao, giúp sản phẩm trông sang trọng hơn. Các ứng dụng phổ biến bao gồm phần cứng trang trí cho túi xách, giày dép, quần áo và phụ kiện phòng tắm.
Mạ điện bảo vệ: Được sử dụng cho các bộ phận như vít, khóa canvas và phần cứng xây dựng, loại này chủ yếu để cải thiện khả năng chống ăn mòn, chống mài mòn và ngăn ngừa rỉ sét. Ví dụ, các vít thường tiếp xúc với môi trường ngoài trời sẽ được hưởng lợi đáng kể từ các biện pháp chống rỉ sét. Kẽm, niken và thiếc là các vật liệu phổ biến nhất được sử dụng trong mạ điện bảo vệ.
Mạ điện đặc biệt: Bạc, đồng và vàng, nổi tiếng với độ dẫn điện tuyệt vời, được sử dụng không chỉ cho mục đích trang trí mà còn cho mạ bảng mạch và các sản phẩm khác để tăng cường độ dẫn điện. Bên cạnh đó, mạ điện đặc biệt còn có thể được sử dụng để tăng khả năng hàn, tăng trở kháng và các yêu cầu cụ thể khác bằng cách phủ bề mặt với lớp kim loại có tính chất đặc biệt.
Quy trình mạ điện
Mạ điện bao gồm nhiều kỹ thuật khác nhau, mỗi kỹ thuật phù hợp với nhu cầu cụ thể và đóng vai trò quan trọng trong việc sản xuất các sản phẩm chất lượng cao. Dưới đây là giới thiệu ngắn gọn về các quy trình mạ điện khác nhau và các ứng dụng của chúng:
Mạ điện bằng giá đỡ
Quy trình này bao gồm việc cố định các vật cần mạ lên một giá đỡ kim loại, phù hợp cho các vật nhỏ, phức tạp và có độ chính xác cao như các bộ phận phần cứng chính xác, kết nối pin lithium và các thành phần bán dẫn.
Mạ điện bằng thùng quay
Các bộ phận nhỏ được đặt trong một thùng kim loại quay để tạo lớp phủ đều, chủ yếu được sử dụng cho sản xuất hàng loạt các bộ phận phần cứng nhỏ như vít, đai ốc, bu lông và các linh kiện ô tô, rất hiệu quả trong việc xử lý bề mặt cho các bộ phận ô tô.
Mạ điện bằng giường tầng sôi
Quy trình này sử dụng một lớp các hạt rắn được làm đầy bằng dung dịch điện phân. Các vật được đặt trong giường này sẽ được phủ đều, phù hợp cho các vật nhỏ, có hình dạng phức tạp, đặc biệt là những vật cần gia công với hình dạng chi tiết.
Mạ điện liên tục trên dải kim loại
Dải kim loại phẳng được đưa liên tục qua bể điện phân, tạo ra lớp phủ đồng đều, thường được sử dụng trong sản xuất các linh kiện điện tử như bảng mạch in (PCB) và các đầu nối, cũng như các lớp bảo vệ cho phần cứng dải kim loại.
Mạ điện treo
Các vật được treo trong dung dịch điện phân thay vì được cố định trên giá, áp dụng cho các vi thành phần cần xử lý bề mặt chính xác cao, như vi cảm biến, vi thấu kính trong các thiết bị MEMS hoặc các thiết bị y tế cấy ghép.
Mạ điện bằng lắng đọng hơi
Sử dụng phương pháp lắng đọng điện hóa để tạo ra các lớp mạ mỏng, phù hợp cho các lớp phủ màng mỏng phức tạp như lớp phủ quang học và các quy trình màng mỏng trong ngành công nghiệp bán dẫn để sản xuất mạch tích hợp (IC).
Mạ điện cuộn
Quá trình này bao gồm việc cho bề mặt vật liệu liên tục đi qua bể điện phân để mạ đều, được sử dụng để tạo lớp bảo vệ trên các dải kim loại và vật liệu trang trí trong xây dựng.
[4]
Ứng dụng của lưu lượng kế (flow meters) và vòi phun trong ngành công nghiệp mạ điện
Ứng dụng của lưu lượng kế (flow meters) và vòi phun trong ngành công nghiệp mạ điện: Trong ngành mạ điện, chất lượng của lớp mạ chịu ảnh hưởng lớn bởi các yếu tố như lượng và phân bố dung dịch mạ được phun, thời gian tiếp xúc giữa dung dịch và vật liệu, và lực tác động của dung dịch lên bề mặt. Điều này làm cho chất lượng và hiệu suất của vòi phun trở nên quan trọng trong quá trình mạ điện.
Ngoài ra, các quy trình tiền xử lý như làm sạch bề mặt vật liệu trước khi mạ và rửa trong quá trình mạ cũng được thực hiện bằng cách phun vòi. Các bể mạ thùng cũng yêu cầu vòi phun để làm sạch. Lưu lượng kế và vòi phun đóng vai trò then chốt trong ngành mạ điện; vòi phun được sử dụng rộng rãi trong các quy trình tiền xử lý để nâng cao chất lượng lớp mạ, trong khi lưu lượng kế đo lượng dung dịch mạ sử dụng, hỗ trợ kiểm soát hiệu quả quá trình sản xuất.
[5]
Ứng dụng 1: Quy trình rửa thiết bị mạ điện – Vòi phun góc rộng áp suất thấp
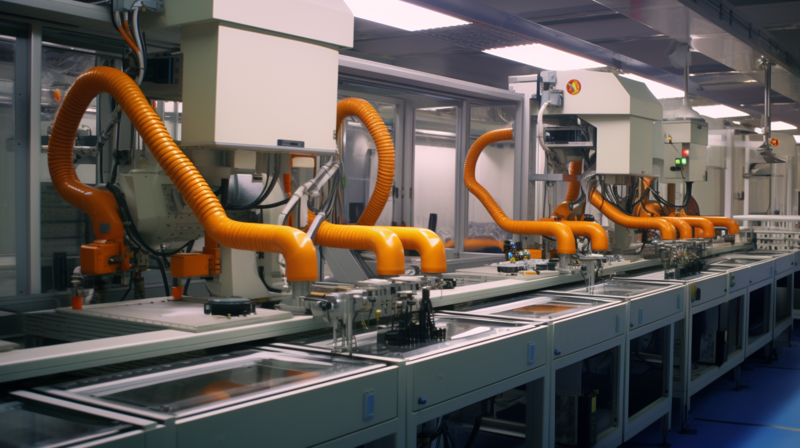
Trường hợp điển hình: Một nhà sản xuất thiết bị PCB nổi tiếng của Đài Loan
chuyên về nghiên cứu và phát triển thiết bị tự động cho bảng mạch, bao gồm thiết bị mạ điện dọc, máy móc bảng mạch ngang và các thiết bị quang điện. Trong thiết bị mạ điện của họ, quy trình rửa rất quan trọng để tránh làm hỏng bề mặt bảng mạch, do đó cần sử dụng dòng nước áp suất thấp để làm sạch. Công ty đã tìm kiếm một loại vòi phun có khả năng phun trên diện rộng ngay cả ở áp suất thấp.
Giải pháp: Vòi phun dòng D Clamp của LORRIC
Các vòi phun hình quạt góc rộng áp suất thấp này sử dụng bề mặt phản xạ bên ngoài lỗ phun để đạt được thiết kế phun hiệu quả ngay cả trong môi trường áp suất thấp. Chúng có thể tạo ra vùng làm sạch rộng hơn 145 độ, mang lại hiệu suất rửa hiệu quả. Ngoài ra, dòng D Clamp có kiểu gắn kẹp ống, dễ dàng lắp đặt và cấu trúc đa phần, giúp người dùng bảo trì và thay thế dễ dàng.
Ứng dụng 2: Giám sát lưu lượng & Giao tiếp điều khiển trung tâm trong thiết bị mạ điện
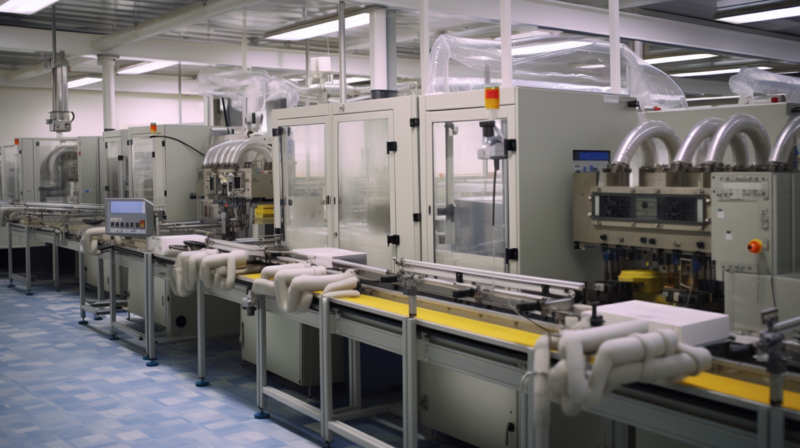
Trường hợp điển hình: Một nhà sản xuất thiết bị tự động hóa nổi tiếng của Đài Loan
chuyên về quy trình DES cho bảng mạch in, máy cắt bavia, và thiết bị mạ điện cho bảng mạch và phần cứng kim loại, đã gặp phải một thách thức. Việc đo lường chính xác chất lỏng và khí là điều cần thiết cho thiết bị mạ vàng và thiếc của họ. Ngoài ra, các máy mạ điện của họ yêu cầu lưu lượng kế (flow meter) để truyền tín hiệu giao tiếp với bảng điều khiển trung tâm.
Giải pháp: Lưu lượng kế loại diện tích F22 và lưu lượng kế cánh quạt FP-AS510 của LORRIC
Để đo lượng nước và khí sử dụng trong thiết bị mạ điện, lưu lượng kế phao kiểu diện tích của LORRIC được đề xuất, đảm bảo độ chính xác trong khoảng ±5% F.S. Thang đo lưu lượng trên thân chính được khắc laser, dễ nhận biết tại chỗ và bền bỉ. Để giao tiếp với bảng điều khiển trung tâm, lưu lượng kế cánh quạt FP-AS510 AxleSense của LORRIC đã được gợi ý. Thiết bị này cung cấp ba định dạng giao tiếp: đầu ra analog 4-20mA, tín hiệu điều khiển Modbus RTU RS485, và tín hiệu chuyển đổi quang điện (tín hiệu xung), mang đến các tùy chọn giao tiếp toàn diện cho người dùng.
Ứng dụng 3: Giám sát lưu lượng hóa chất mạ điện
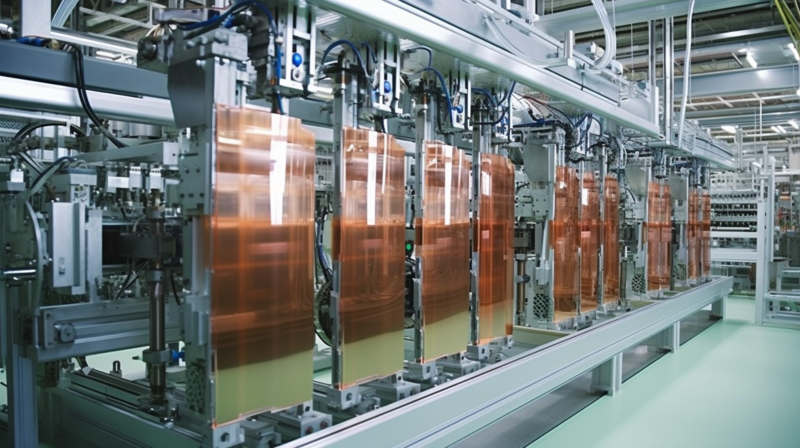
Giám sát lưu lượng trong dây chuyền mạ liên tục dọc
Trường hợp điển hình: Một nhà sản xuất PCB nổi tiếng của Đài Loan: Công ty sử dụng dây chuyền mạ liên tục dọc trong sản xuất, giúp tăng cường hiệu quả phân phối trong quá trình mạ điện và duy trì chất lượng đồng nhất cho tất cả các bảng mạch. Thiết bị mạ liên tục dọc sử dụng nhiều loại hóa chất, do đó cần các lưu lượng kế (flow meter) có khả năng giám sát hiệu quả lượng hóa chất sử dụng và có khả năng chống ăn mòn.
Giải pháp: Lưu lượng kế loại diện tích F201 và lưu lượng kế cánh quạt FP-AS510 của LORRIC
Lưu lượng kế loại diện tích của LORRIC được làm từ nhựa chất lượng cao, có khả năng chống chịu mạnh mẽ với các dung dịch hóa chất ăn mòn, từ đó giảm tần suất bảo trì và tiết kiệm chi phí. Ngoài ra, để giám sát hiệu quả lượng hóa chất sử dụng trong thiết bị mạ điện, các lưu lượng kế có khả năng giao tiếp là điều cần thiết. Để đáp ứng yêu cầu về đầu ra giao tiếp của khách hàng, lưu lượng kế cánh quạt FP-AS510 của LORRIC là giải pháp tối ưu. Sản phẩm này có ba đầu ra giao tiếp (đầu ra analog 4-20mA, tín hiệu điều khiển Modbus RTU RS485 và tín hiệu chuyển đổi quang điện (tín hiệu xung)), tương thích với các định dạng giao tiếp của thiết bị điều khiển nội bộ.