1. PCB(인쇄 회로 기판)이란 무엇인가?
인쇄 회로 기판(Printed Circuit Board, PCB)은 전자 부품을 연결하는 기판으로, 현대 전자 산업에서 없어서는 안 될 중요한 부품입니다. 스마트폰, 가전제품, 산업 자동화 시스템 등 거의 모든 전자 제품에 PCB가 사용됩니다. 복잡한 전자 장비는 여러 전자 부품이 함께 작동해야 하는데, PCB는 이들 부품을 한데 모아주는 플랫폼 역할을 합니다.
즉, PCB는 많은 전자 부품과 회로가 있는 얇은 판입니다. 우리가 자주 듣는 IC보드(Integrated Circuit, 집적 회로 보드)는 집적 회로와 기타 부품이 통합된 완전한 회로 기판을 의미하며, 보통 IC보드는 PCB 위에 납땜됩니다. PCB의 전도층을 통해 서로 다른 전자 부품 간에 전류와 신호가 전달되어 전자 시스템을 구축할 수 있으며, 이를 통해 전자 제품의 특정 기능을 구현할 수 있습니다.
[1][2]
2. AI 서버가 PCB 수요를 촉진하는 방법
ChatGPT와 같은 생성형 AI 산업의 빠른 확장으로 고성능 AI 서버에 대한 수요가 급증하고 있습니다. 이러한 서버는 고속 처리를 위해 고급 PCB(인쇄 회로 기판)가 필요하며, 그에 따라 ABF(아지노모토 빌드업 필름) 기판과 고층 PCB(HLC)의 수요가 증가하고 있습니다.
ABF 기판은 고밀도 상호 연결(HDI) PCB를 제조하는 데 필수적이며, 미세 라인, 블라인드 비아 및 매립 비아를 통해 복잡하고 컴팩트한 회로를 지원하여 제한된 공간에서 높은 통합을 가능하게 합니다. 또한, HLC PCB는 복잡한 회로와 고밀도 연결을 수용할 수 있는 인프라를 제공하여 AI 서버의 높은 계산 요구를 충족하는 데 필수적입니다.
[3]
3. EV 전기차가 이끄는 자동차용 PCB 산업
최근 몇 년간 자동차는 계속해서 전자화되는 추세로 발전하고 있으며, 전기차(Electric Vehicles, EV)의 보급이 자동차용 PCB 산업의 성장을 촉진하고 있습니다. 국제 데이터 정보(IDC)에 따르면, 2022년 전 세계 전기차 시장은 약 1,100만 대에 이르렀고, 이에 따라 자동차용 PCB에 대한 수요도 증가했습니다.
자율주행 및 스마트 콕핏 기술이 지속적으로 업그레이드되고, 5G 고속 통신에 대한 요구가 증가함에 따라 차량의 기능 설계가 점점 더 복잡해지고 있습니다. 또한 차량 기능을 제어하는 ECU(Electronic Control Unit)의 수가 늘어나고 있으며, ECU의 구성 요소 중에는 PCB가 포함되어 있습니다. 성능이 더 강력하고 다기능의 ECU를 제조하려면 PCB 사용량과 기술적 요구도 함께 증가하고 있습니다.
[4]
4. Printed Circuit Board (PCB)의 종류
Printed Circuit Boards(PCBs)는 많은 전자 부품들이 장착되어 있으며, 일반적으로 구리 트레이스를 사용하여 이 부품들 간의 통신을 연결하는 매개체 역할을 합니다. 제품의 특성 및 용도에 따라, PCBs는 다양한 유형으로 분류됩니다:
1. 단면 PCB - 이 유형의 PCB는 한쪽에만 도전성 층이 있고, 반대쪽은 다양한 전자 회로를 통합하는 데 사용됩니다. 전자 계산기, 라디오와 같은 단순한 전자 제품에 자주 사용되며, 비용이 비교적 저렴합니다.
2. 양면 PCB - 양면 PCB는 기판의 양쪽에 도전성 층이 존재하며, 절연층으로 분리됩니다. 양쪽의 부품은 도금된 통로(Plated Through Hole)를 통해 연결되며, 이를 통해 더 컴팩트한 회로 설계가 가능합니다. 이 유형은 디지털 카메라, 측정 장비, 게임 컨트롤러와 같은 중간 복잡도의 전자 장비에 적합합니다.
3. 다층 PCB - 다층 PCB는 여러 층의 구리 포일이 절연 재료로 분리되어 있으며, 모두 고압과 고온으로 결합되어 내구성을 제공합니다. 다층 PCB는 높은 통합 및 복잡한 회로 설계를 가능하게 하며, 데이터 저장 장치, 위성 시스템, 의료 기기, GPS 장비와 같은 고급 전자 제품에 이상적입니다.
4. Rigid PCB - 하드 PCB라고도 알려진 이 유형은 일반적으로 유리 섬유 강화 에폭시 수지(FR-4)를 기본 재료로 사용합니다. Rigid PCB는 강도가 높고 유연하지 않으며, 컴퓨터 마더보드의 중앙 처리 장치(CPU), 의료 모니터링 장비 및 산업 자동화 장비에 일반적으로 사용됩니다.
5. Rigid-Flex PCB - Rigid-Flexible Printed Circuit Boards 또는 Rigid-Flex 보드로 알려진 이 유형은 Flex 커넥터를 통해 서로 연결된 강성과 유연한 부분을 결합합니다. 정밀한 정렬과 적층이 결합을 위해 필수적이며, 도금된 통로(PTH)를 사용하여 다층 연결을 달성합니다. Rigid-Flex PCBs는 접이식 장치 및 임베디드 의료 장비에 사용됩니다.
6. Flexible PCB - Flex PCB로 자주 언급되며, 폴리에스터 또는 폴리이미드 필름과 같은 유연한 기판 재료를 사용하여 제작됩니다. 유연성과 가벼운 특징을 가지며, 생산 비용이 더 높고 디스플레이, 스마트워치, 항공우주 장비 패널 및 엔터테인먼트 시스템과 같은 공간 제약이 있는 응용 프로그램에 적합합니다.
7. 고주파 PCB - 고주파 신호 및 마이크로파 응용 프로그램을 위해 설계된 이 PCB는 전자기 간섭(EMI) 및 무선 주파수 간섭(RFI)으로 인한 신호 반사를 방지하기 위해 임피던스 제어가 필요합니다. 고주파 PCB는 디자인과 제조에서 고급 기술이 요구되며, 무선 통신 장치 및 레이더 시스템에 자주 사용됩니다.
8. HDI PCB(High-Density Interconnect PCB) - 이 PCB는 미세 비아(Microvia), 블라인드 비아(Blind Via), 매립 비아(Buried Via) 및 BGA 패키징을 활용하여 높은 통합 및 밀집된 연결을 달성합니다. HDI PCB는 고성능 전자 장치, 예를 들어 스마트폰, 태블릿 및 고급 통신 장치에 사용되며, 소형화, 경량화 및 성능 향상 요구를 충족시킵니다.
9. Metal Core PCB - 전통적인 유리 섬유 대신 금속을 기본 재료로 사용하며, Metal Core PCB는 우수한 열 발산 성능을 제공합니다. 이들은 주로 LED 조명 및 태양광 변환기와 같은 고온 응용 프로그램에 사용됩니다.
[5][6][7]
5. PCB(인쇄 회로 기판) 제조 공정
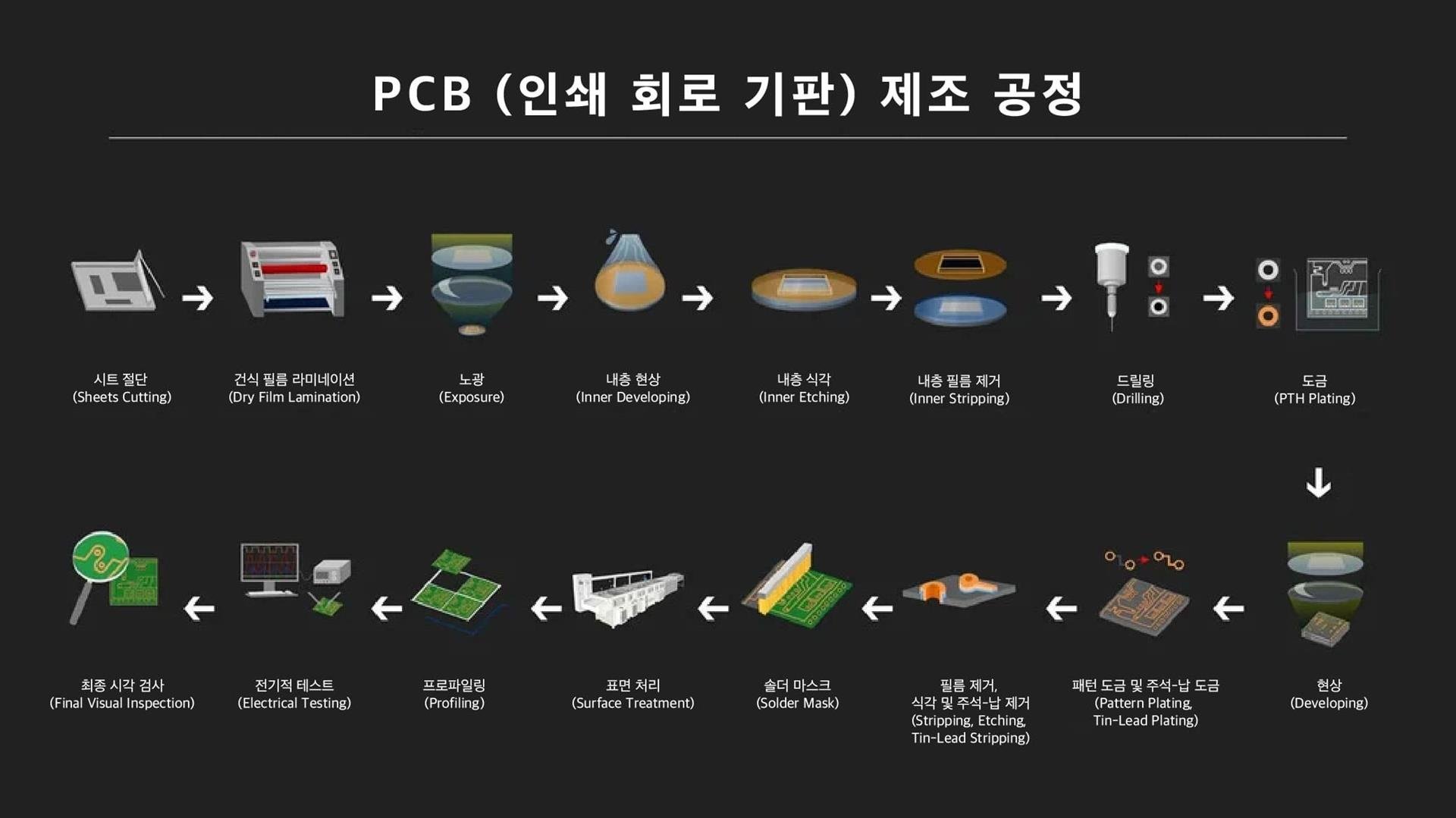
STEP 1: 시트 절단 (Sheets Cutting)
기판을 필요한 크기로 절단합니다.
STEP 2: 건식 필름 라미네이션 (Dry Film Lamination)
기판 표면을 감광성 유기 필름으로 덮고 노광 후 필름에서 회로 패턴을 기판으로 전사합니다.
STEP 3: 노광 (Exposure)
드라이 필름이 부착된 기판을 노광 기계에 넣어 노광을 진행합니다. 필름의 투명한 영역에 UV 빛이 노출되면 드라이 필름이 감광성 경화를 거칩니다. 이 과정에서 회로 이미지가 필름에서 기판 표면으로 전사됩니다.
STEP 4: 내층 현상 (Inner Developing)
비감광성 드라이 필름을 현상액에 용해시켜 내부층 회로 패턴을 형성합니다.
STEP 5: 내층 식각 (Inner Etching)
미현상 드라이 필름이 용해되면 기판의 하부에 있는 구리 표면이 노출됩니다. 이후 보드는 에칭 공정을 거쳐, 노출된 구리 표면이 에칭액에 의해 용해되어 기판이 드러나게 됩니다. 드라이 필름이 부착된 구리 표면은 그대로 유지되어 내부 회로를 형성합니다.
STEP 6: 내층 필름 제거 (Inner Stripping)
현상된 드라이 필름은 필름 제거액을 사용하여 제거합니다.
STEP 7: 드릴링 (Drilling)
PCB 드릴링 과정에서는 여러 유형의 홀(관통 홀, 매립 홀, 맹홀, 마이크로홀 등)이 형성되며, 구성 요소 및 기계적 홀도 포함됩니다. 이러한 홀들은 높은 정확성이 요구되므로 수동 드릴이나 레이저 PCB 드릴을 사용하여 일반적으로 제작됩니다.
STEP 8: 도금(PTH Plating)
관통 홀 전기 도금(일명 원샷 구리 도금)은 비전도성 수지나 유리 섬유 홀 내부에 얇은 구리층을 화학적으로 증착하는 과정입니다. 이 과정은 홀 벽을 금속화하여 내부 회로층과 외부 회로층 간의 연결을 가능하게 합니다.
STEP 9: 현상 (Developing)
회로 기판의 외층에 남아 있는 노출되지 않은 드라이 필름을 현상액에 용해하는 과정입니다.
STEP 10: 패턴 도금 및 주석-납 도금 (Pattern Plating, Tin-Lead Plating)
현상 후, 다음 단계는 외층 회로의 두께를 증가시키기 위해 이중 구리 도금과 주석-납 도금을 진행하는 것입니다. 주석 도금의 목적은 이후 에칭 공정에서 에칭 용액에 의해 구리가 용해되는 것을 방지하기 위함입니다.
STEP 11: 필름 제거, 식각 및 주석-납 제거 (Stripping, Etching, Tin-Lead Stripping)
보호층 역할을 했던 주석-납 도금이 제거액에 의해 제거되어 보드 표면의 구리층이 드러납니다. 에칭액을 사용한 후, 노출된 구리층은 용해되고 기판이 드러납니다. 주석으로 도금된 구리 표면은 주석의 보호층 덕분에 영향을 받지 않고, 최종적으로 외부 회로가 형성됩니다. 마지막으로, 보드 표면에 남아 있는 모든 주석-납 도금은 주석-납 제거액을 사용하여 제거됩니다.
STEP 12: 솔더 마스크 (Solder Mask)
전처리 후 보드는 세척되고, 표면에 솔더 레지스트 감광 잉크가 도포됩니다. 예비 건조 과정을 거친 후, 노광 작업이 진행됩니다. 노광 후, 감광되지 않은 솔더 레지스트 잉크는 현상액에 의해 용해되지만, 노출로 경화된 감광 솔더 레지스트 잉크는 영향을 받지 않고 보드 표면에 솔더 마스크 패턴을 형성합니다.
STEP 13: 표면 처리 (Surface Treatment)
목적은 표면 산화를 방지하는 것입니다.
STEP 14: 프로파일링 (Profiling)
외부 가공 및 절단을 수행하여 고객 요구 사항에 맞는 크기로 만듭니다.
STEP 15: 전기적 테스트 (Electrical Testing)
외부 가공 및 절단을 수행하여 고객 요구 사항에 맞는 크기로 만듭니다.
STEP 16: 최종 시각 검사 (Final Visual Inspection)
제품의 외관을 종합적으로 검사하여 출하되는 제품의 품질을 보장합니다.
6. PCB 산업에서 노즐과 유량계의 적용
인쇄 회로 기판(PCB) 제조에는 전기도금, 현상, 식각 및 세척과 같은 여러 정밀한 공정이 포함되며, 이 모든 과정에서 정확한 화학 처리제가 필요합니다. 이러한 공정에서는 분사되는 화학 물질의 양과 분포, 액체가 재료와 접촉하는 시간, 화학 물질이 기판에 미치는 압력 등이 최종 제품 품질에 중요한 영향을 미칠 수 있습니다. 따라서 고품질의 노즐을 사용하여 균일한 분사가 이루어지는 것이 매우 중요합니다. 또한 유량계를 사용하여 화학 처리제의 양을 모니터링하고 제어하면 재료 사용을 최적화할 수 있어 제품 품질을 향상시키고 전반적인 생산 효율성을 높일 수 있습니다.
응용 1: 관통홀 전해 도금에서 도금 잔여물 제거를 위한 액체 스프레이

사례: 세계적으로 유명한 전자 장비 통합 제조업체
상황: 이 회사는 **수평 화학 구리 도금 장비(DSM & PTH)**를 개발하여, 관통홀 전해 도금 후 회로 기판 구멍에 남아있는 접착제 잔여물을 효과적으로 제거함으로써, 이후 생산 단계에서 최적의 전도 성능을 보장합니다. 이 잔여물을 제거하기 위해 다양한 화학제를 사용해야 하며, 이에 따라 회사는 내식성이 뛰어난 효율적인 노즐을 필요로 했습니다.
해결책: LORRIC의 QF 시리즈 퀵 디스커넥트 노즐
고품질의 엔지니어링 플라스틱(PP, PVDF)으로 제작되어 뛰어난 내화학성을 제공하며, 노즐의 수명을 연장합니다. 또한, QF 시리즈 노즐은 다중 파트 퀵 디스커넥트 설계로, 노즐을 설치한 후 교체가 필요할 경우 베이스에서 헤드만 분리하여 교체할 수 있습니다. 이를 통해 노즐의 재배치를 할 필요 없이 장비 유지 관리와 서비스 절차를 간소화합니다.
응용 2: 전해 도금 공정에서 황산구리 용액 모니터링

사례: 대한민국 상위 10대 PCB 제조업체
상황: 1987년에 설립된 이 회사는 DRAM 메모리 칩 모듈 PCB 및 다양한 반도체 칩 조립 공정을 위한 기판을 개발하는 데 특화된 기업입니다. 2022년 기준으로 대한민국에서 상위 10대 인쇄 회로 기판(PCB) 공급업체 중 하나로 자리 잡았습니다. 초기에는 독일 브랜드의 패들휠 유량계를 사용하여 전해 도금 공정 라인에서 황산구리 용액의 사용량을 측정했습니다.
해결책: LORRIC의 FP-AS510 패들휠 유량계
FP-AS510 패들휠 유량계는 듀얼 LED/LCD 화면 설계를 특징으로 하여, 작업자들이 낮은 조명 조건이나 투명 칸막이 구역을 통해서도 쉽게 **유량을 읽고 장비 상태를 모니터링**할 수 있습니다. 또한, FP-AS510은 특허 받은 축 감지 기술**을 사용하여 매우 낮은 속도(0.15 m/s)에서도 유량을 감지할 수 있으며, 0.5% FS의 업계 최고 수준의 선형성을 제공합니다.
이 유량계는 3가지 통신 옵션(4-20mA 아날로그 출력, Modbus RTU RS485 제어 신호, 옵토커플러 펄스 신호)을 지원하여, 다양한 고객의 통신 요구 사항을 원활하게 충족시킵니다. 이를 통해 회사는 안전 규정을 준수하면서도 정확한 유량 모니터링을 가능하게 합니다.
응용 3: 수직 연속 도금 장비에서 강산 및 강알칼리 용액 모니터링
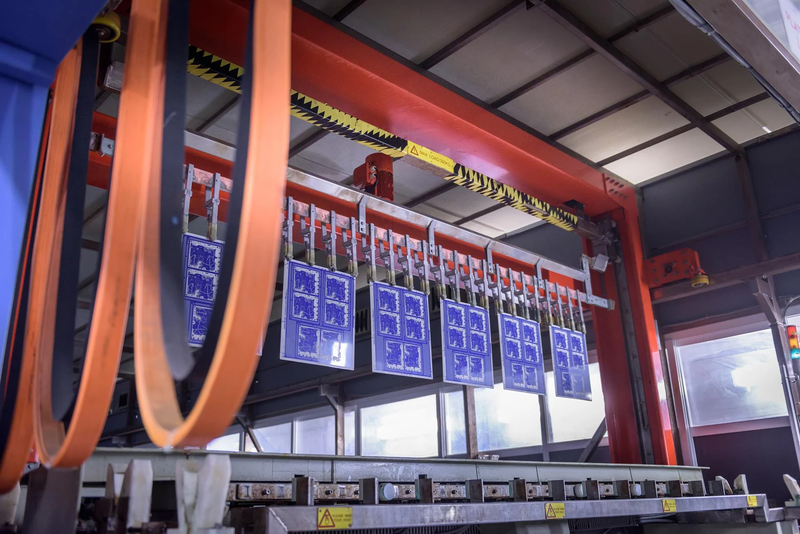
사례: 세계 5대 PCB 제조업체
상황: 이 회사는 수직 연속 도금 라인을 사용하여 도금의 분포 효율을 크게 향상시키고 각 패널의 일관된 도금 품질을 유지합니다. 이 라인에서는 다양한 화학제를 사용하며, LORRIC의 유량계는 내화학성이 강한 고품질 플라스틱으로 제작되어 강산 및 강알칼리 용액을 다루면서도 장비의 유지 관리 빈도와 비용을 효과적으로 줄여줍니다.
해결책: FU-ES EchoSense 클램프형 초음파 유량계
PCB의 정밀도 요구가 증가함에 따라, 많은 제조업체는 화학 용액과 직접 접촉하지 않는 초음파 유량계를 선호하고 있습니다. 이를 해결하기 위해, LORRIC은 새로운 FU-ES EchoSense 클램프형 초음파 유량계를 개발했습니다. 이 제품은 소구경 애플리케이션에 맞춰 설계되었으며, 통합된 디자인으로 90초 안에 신속한 설치가 가능합니다.