In the face of escalating water consumption charges, industries such as electricity, steel, textile, and cement are under increasing pressure to adapt and mitigate their environmental impact. The urgency of this issue is underscored by the significant carbon footprint and energy consumption of these sectors, which are crucial to modern economies but also among the largest contributors to CO2 emissions globally.
Steel Industry
For the steel industry, which is responsible for approximately 7-9% of anthropogenic CO2 emissions, transitioning to greener alternatives like "green" hydrogen and recycling materials can help reduce its carbon footprint. The iron and steel sector, as a pivotal component of the construction and manufacturing industries, faces the dual challenge of meeting growing demand while also pursuing decarbonization.
Cement Industry
The cement industry, another major water consumer, is responsible for almost 7% of global emissions. This industry's high energy requirements for processes such as clinker production make it a significant focus for emission reduction efforts. Innovative technology solutions and the adoption of circular economy approaches are essential for the cement industry to reduce its carbon footprint and water usage.
Textile Sector
In the textile sector, the challenge is twofold: reducing both energy and water consumption. The industry is one of the largest consumers of water in manufacturing, making it a critical area for implementing water efficiency measures. Technologies and practices that improve water treatment and recycling can significantly mitigate the environmental impact of textile production
[1][2]
Implementing energy efficiency measures across these industries is vital. For steel and cement sectors, adopting best available technologies (BATs) can lead to substantial energy savings and reduced CO2 emissions. The IEA's global benchmarking project highlights the potential for significant efficiency gains in the iron, steel, and cement sub-sectors through the adoption of BATs, optimized processes, and waste heat recovery[3]
To assist industries in reducing water consumption fees, several strategies can be employed:
Strategy 1: Implementing Energy and Water Efficiency Measures
Adopting best available technologies (BATs) for improving both energy and water efficiency is essential. For instance, in the steel and cement sectors, energy-efficient kilns and waste heat recovery systems can significantly reduce water consumption by lowering the overall energy demand. [2]
Strategy 2: Recycling and Material Reuse
Circular economy practices, including the use of recycled materials, can drastically reduce the demand for raw materials and the associated water usage. The steel industry, for example, can leverage "green" hydrogen and increase the recycling of scrap metal to minimize water usage.
Strategy 3: Advanced Water Recycling and Treatment
Closed-loop water recycling systems and advanced water treatment technologies enable industries to reuse water, significantly cutting down freshwater extraction and reducing water pollution. [1]
Strategy 4: Transitioning to Renewable Energy
Switching to renewable energy sources for industrial processes can indirectly reduce water consumption by lowering the reliance on water-intensive fossil fuel extraction and processing.
Strategy 5: Optimizing Production Processes
Process optimization can lead to significant water savings, such as adopting precision techniques in the textile industry for water-intensive processes like dyeing and finishing. [2]
Case Study: The Textile Industry's Shift - Sustainable Water Management
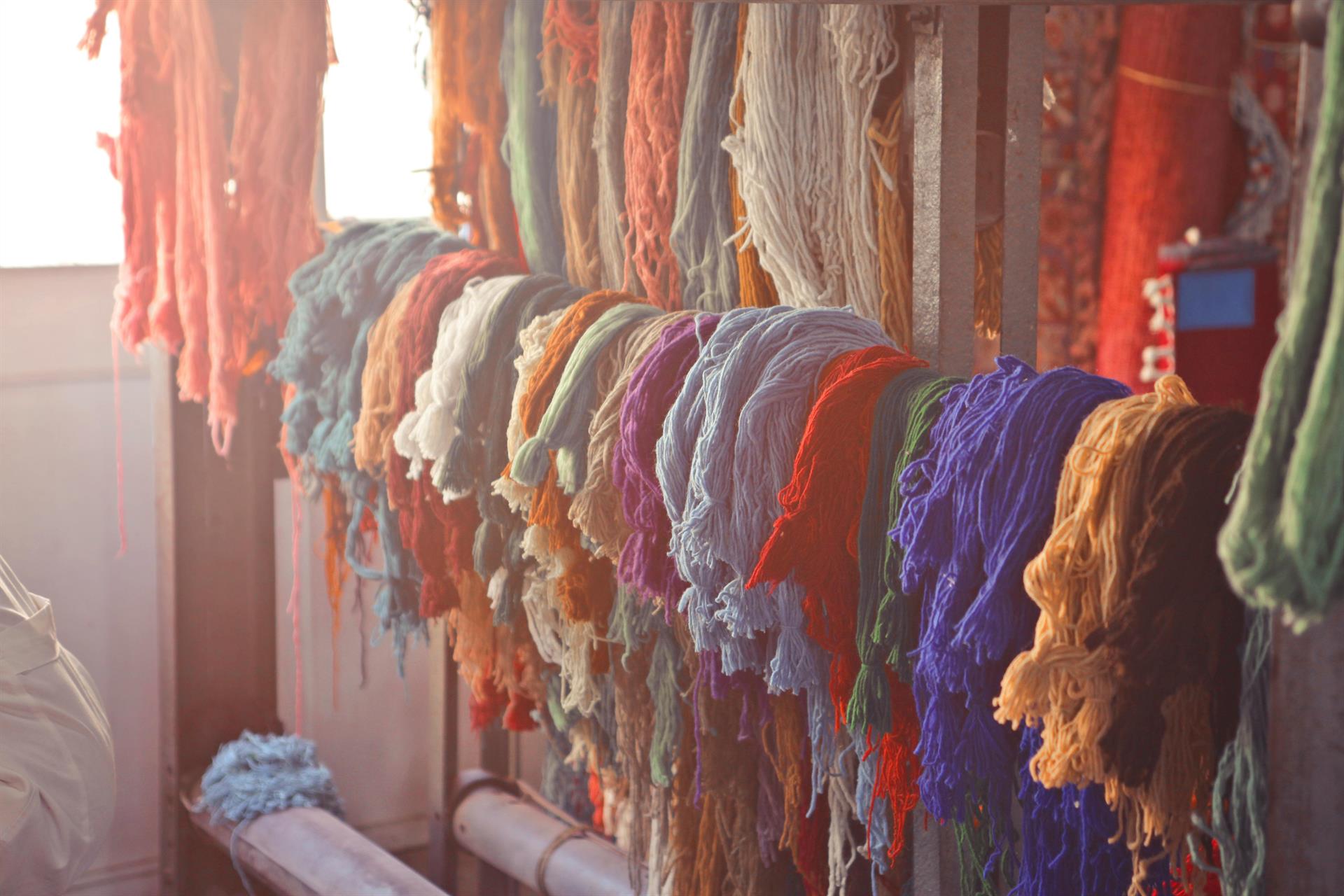
The textile industry has seen initiatives like the Clean By Design program by the Natural Resources Defense Council, which works with apparel brands to leverage buyer power to clean up factories in their supply chains. By adopting best practices for saving water, electricity, and fuel, participating mills were able to reduce water use by as much as 36%, saving approximately $500,000 annually. [3]