Overview
- Understanding the principles behind various flow meters is crucial for fluid monitoring. This article introduces the working principles of a variety of flow meters, including ultrasonic, variable area, Coriolis, paddle wheel, positive displacement, vortex, turbine, differential pressure, laminar flow, electromagnetic, and thermal mass flow meters. These meters utilize different physical phenomena and technologies, suitable for a wide range of fluid measurement applications.
Flow meters are widely used and versatile instruments in fluid processing systems, from agricultural chemical production to water treatment facilities. They monitor operational efficiency and provide data to detect potential pipeline issues. This article focuses on understanding the working principles of different flow meters. For information on their pros, cons, and selection tips, refer to "
Flowmeter Selection Guide - The Pros and Cons of 11 Types of Flowmeters"
Ultrasonic Flow Meters
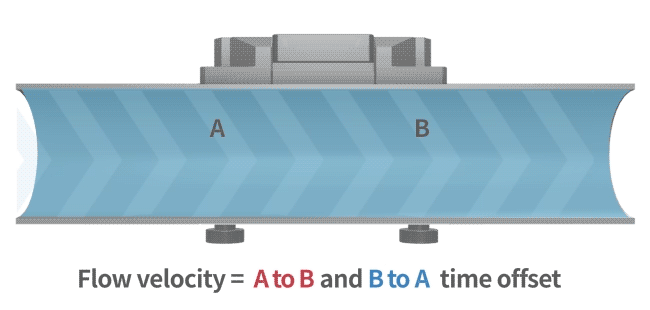
Installed on opposite sides of the pipe wall, ultrasonic flow meters calculate flow rate by measuring the time difference proportional to the flow velocity between the ultrasonic signals transmitted between two probes (sensors) in both downstream and upstream directions. The accuracy of ultrasonic flow meters heavily depends on the installation of the probes. LORRIC's patented probe brackets significantly enhance the convenience and reliability of probe installation.
→ See LORRIC's Ultrasonic Flow Meters
[1]
Variable Area Flow Meters (Rotameters)
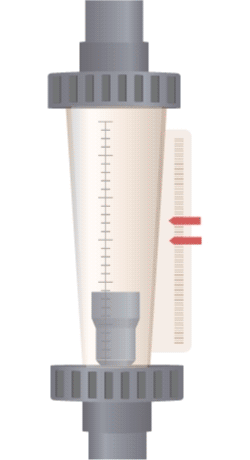
A float suspended in a conical tube (wider at the top and narrower at the bottom) finds its stable equilibrium area where the upward force generated by the pressure difference as fluid passes through balances with the weight of the float. As the flow increases, the float rises to a higher position where a larger cross-sectional area provides enough force to balance the float's weight. Therefore, variable area flow meters (rotameters) measure flow rate by the change in cross-sectional area of the equilibrium zone as liquid passes through.
→See LORRIC's Variable Area Flow Meters
[2]
Coriolis Flow Meters
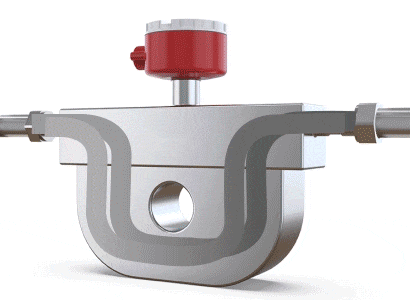
A Coriolis flow meter measures mass flow rate by leveraging the physical phenomenon of Coriolis force (where a particle moving in a straight line within a rotating system, and not parallel to the rotation, experiences a deviation in its trajectory due to the system's inertia). When fluid flows through a U-shaped tube, the Coriolis force causes the tube to twist slightly and vibrate. The difference in flow direction between the inlet and outlet leads to a twisting of the U-shaped tube. Sensors placed near the inlet and outlet detect and calculate these vibrations. By analyzing the amplitude and frequency of the vibrations, the mass flow rate and fluid density can be determined, making it a flow meter specifically for mass flow measurement.
▪ LORRIC offers a wide variety of flow meters,
feel free to leave us a message for consultation!
[3]
Paddle Wheel Flow Meters
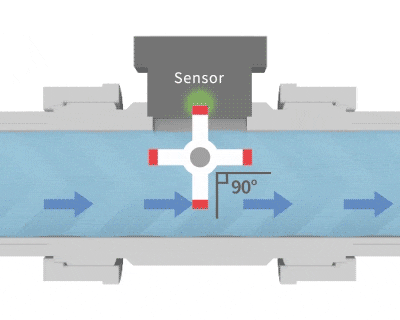
Similar to a water wheel structure, the fluid passes through, causing it to rotate. By embedding magnetic metal substances on the blades, a pulse signal can be extracted. Sensors detect these pulses to calculate the rotation cycles, subsequently converting the flow velocity into flow rate. Paddle wheel flow meter calculation method: Instantaneous flow rate = Pulse flow rate x Number of pulses / Time.
→See LORRIC's Paddle Wheel Flow Meters
[4]
Positive Displacement Flow Meters
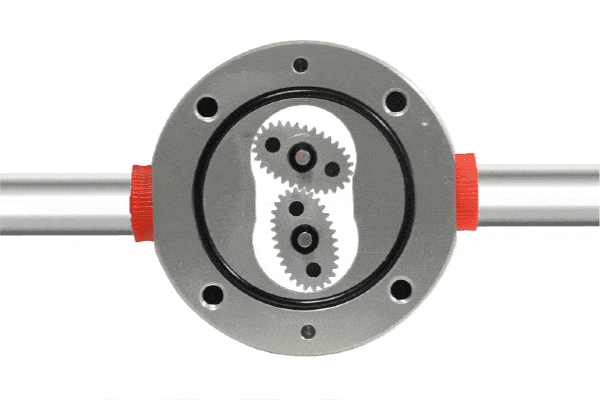
These meters measure flow by repeatedly calculating the volume of fluid passing through a fixed small volume space (commonly referred to as the measuring chamber) inside the meter. Designed with gears (rotating components) within this measuring chamber, a pressure difference generated at the fluid inlet/outlet drives the gears to rotate, continuously directing fluid towards the outlet. Since the volume of the measuring chamber is fixed, the number of gear rotations directly correlates with the volume of fluid passing through the meter. Typically, gears must be highly resistant to chemicals, and positive displacement flow meters are known for their significant pressure drop capability, suitability for high-viscosity liquids, and high accuracy.
[5]
Vortex Flow Meters
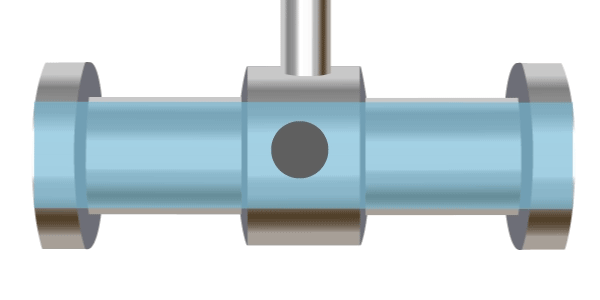
Based on the principle of the Kármán vortex street, named after Theodore von Kármán, who theoretically described it in 1912, vortex flow meters measure flow by creating vortices behind a bluff body placed in the flow path. The vortices' frequency is proportional to the flow velocity, usually measured using ultrasonic methods, allowing for flow calculation.
[6]
Turbine Flow Meters
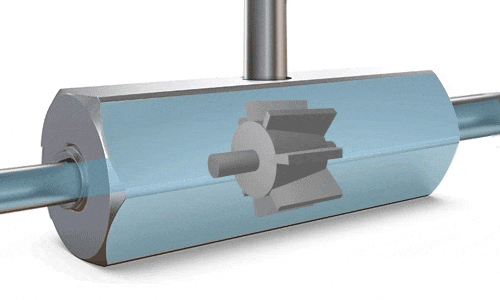
A turbine placed in the center of the meter's diameter rotates as fluid passes through, exerting force on the turbine blades and causing them to spin. When a stable rotational speed is reached, it is proportional to the flow velocity, and magnetic detection yields a pulse signal. Sensors convert this signal to calculate flow rate, with RPM (revolutions per minute) being proportional to flow rate, and the number of revolutions correlating with the total volume passed.
[7]
Differential Pressure Flow Meters
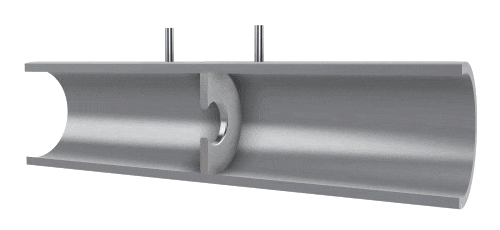
Also known as throttling flow meters, these use the pressure difference created by fluid flowing through a throttling device to determine flow rate. By precisely machining the throttling device and measuring the pressure at the inlet and outlet, the flow rate is determined based on the differential pressure across the throttling device, which also relates to the size of the throttling device.
[8]
Laminar Flow Meters
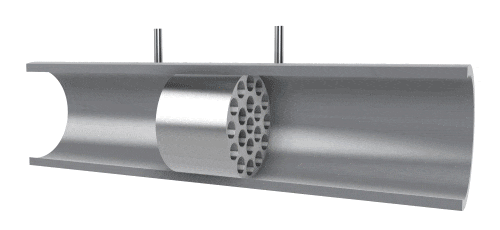
Composed of sensors and a differential pressure gauge, these meters measure flow based on the pressure difference detected by sensors at both ends. The principle is that the adhesive force affects the fluid during flow, causing pressure energy loss. In steady flow, a fixed relationship exists between pressure loss, fluid viscosity, and flow rate, with the differential pressure (△P) being directly proportional to the volumetric flow rate (Qv). They are primarily used to measure small flow rates and high viscosity fluids.
[9]
Electromagnetic Flow Meters
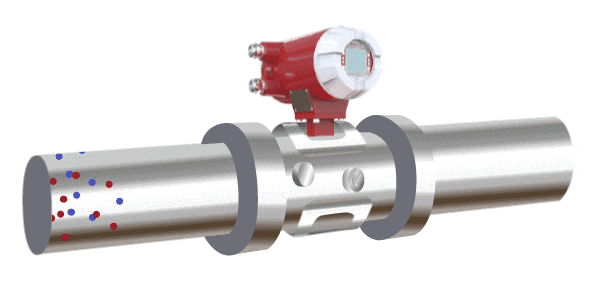
Operating on the principle of electromagnetic induction, electromagnetic flow meters measure the flow of conductive fluids based on the electromotive force generated as the fluid passes through an external magnetic field. Coils installed above the pipeline create a magnetic field, and as the fluid, containing charged ions, passes through, it generates a deflection, producing electromotive force across the sides of the tube, proportional to the average flow velocity, which is then calculated to determine flow rate.
[10]
Thermal Mass Flow Meters
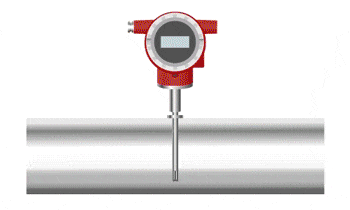
These meters work by placing two tubes (or other heatable objects) within the fluid, heating one of them. As the fluid contacts the heated tube, it carries away heat, causing the fluid temperature to rise. By measuring the temperature change of the fluid passing through both tubes, flow rate is determined. This principle requires more time to reach a stable state.
[11]